Промышленность производство : Курсовая работа: Технология изготовления рычага
Курсовая работа: Технология изготовления рычага
Расчетно-пояснительная
записка к курсовой работе
«Технология
изготовления рычага»
Содержание
1.
Назначение и конструкция детали
2.
Выбор материала детали
3.
Выбор способа формообразования заготовки
4.
Технологический процесс механической обработки «Рычага»
Использованная
литература
1. Назначение и конструкция детали
Деталь «Рычаг» относится к деталям гидромашиностроения и
входит в состав конструкции поворотно-лопастной гидротурбины типа турбины
Каплана. Деталь «Рычаг» является составной частью механизма поворота лопастей
рабочего колеса.
«Рычаг» представляет собой деталь, состоящую из плоской
ступицы диаметром 980 с центральным отверстием диаметром 485 и отходящего от
нее пальца с цилиндрическим галтельным основанием диаметром 250. Рычаг
механизма поворота насаживается на цапфу лопасти (рис. 1 поз.3) посредством
внутреннего отверстия диаметром 485 и скрепляется с цапфой лопасти 7 болтами
М120х4. В конструкции предусматриваются также два цилиндрических штифта
диаметром 130 для передачи крутящего момента от рычага к лопасти. Рычаг
посредством пальца соединяется с серьгой (рис.1 поз.6), которая заменяет шатун,
и шарнирно соединяется вторым своим концом с крестовиной. Крестовина через
проушину и соединительные планки воздействует на рычаг, который, поворачиваясь,
разворачивает лопасть рабочего колеса. Также «Рычаг» удерживает своей боковой
поверхностью лопасть от осевого перемещения.
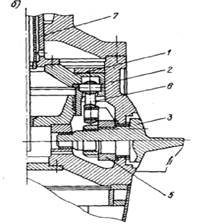
Рис. 1 Разрез рабочего колеса с дифференциальным поршнем:
1-дифференциальный поршень; 2-корпус р.к.; 3-лопасть; 4-цапфа; 5-РЫЧАГ;
6-серьга; 7- контршток сервомотора.
Для транспортировки и кантовки детали на его поверхности
предусмотрено 3 отверстия под рым-болты М30.
2. Выбор материала детали
При работе турбины «Рычаг» подвержен большим нагрузкам:
подвергается одновременному действию усилия, приложенному к его пальцу от
сервомотора, и центробежной силы лопасти, цапфы и самого рычага, поэтому к его
прочности предъявляются высокие требования. Для обеспечения необходимой
прочности рычаг изготавливают из высокопрочных сталей путем ковки с последующей
нормализацией 870-890oC или закалкой 920-950 oC с
отпуском 570-600oC .
Исходя из вышесказанного, в качестве материала рычага
принимаем конструкционную легированную сталь Сталь 30ГСЛ ГОСТ 977-88. Сталь применяется
для деталей типа лопасти гидротурбин, рычаги, фланцы, сектора, венцы зубчатые,
ролики обоймы, колеса ходовые и др., а также фасонные отливки, отливаемые
методом точного литья, зубчатые колеса, бандажи, отливки небольших сечений и
другие детали общего машиностроения к которым предъявляются требования
повышенной твердости, сварно-литых конструкций с большим объемом сварки и др.
Химический состав и механические свойства стали 30ГСЛ необходимо знать для
выбора способа получения заготовки, режимов резания и технического
нормирования.
Таблица 1. Химический состав стали 30ГСЛ ГОСТ 977-88
Химический элемент |
% |
Кремний (Si) |
0.60-0.80 |
Медь (Cu), не более |
0.30 |
Марганец (Mn) |
1.10-1.40 |
Никель (Ni), не более |
0.30 |
Фосфор (P), не более |
0.040 |
Хром (Cr), не более |
0.30 |
Сера (S), не более |
0.040 |
Таблица 2. Механические свойства
Термообработка, состояние поставки |
0,2, МПа |
B, МПа |
5, % |
, % |
KCU, Дж/м2 |
Нормализация 870-890 °С. Отпуск
570-600 °С. |
350 |
600 |
14 |
25 |
29 |
Закалка 920-950 °С. Отпуск 570-650
°С. |
400 |
650 |
14 |
30 |
49 |
Таблица 3. Технологические свойства
Свариваемость |
Способы сварки: РДС, АДС под
газовой защитой, ЭШС. Необходимы подогрев и последующая термообработка. |
Обрабатываемость резанием |
при НВ 156 Ku тв.спл. = 1,0, Ku
б.ст. = 0,8. |
Склонность к отпускной способности |
не склонна |
Флокеночувствительность |
не чувствительна |
Таблица 4. Общие сведения
Заменитель |
стали: 20ГСЛ, 25ГСЛ, 40ХЛ. |
Вид поставки |
отливки ГОСТ 977-75. |
Таблица 5. Литейные свойства
Линейная усадка, % |
1487 |
Показатель трещиноустойчивости,
Кт.у. |
2.2-2.3 |
Жидкотекучесть, Кж.т. |
1.0 |
Склонность к образованию усадочной
раковины, Ку.р. |
0.9 |
Склонность к образованию усадочной
пористости, Ку.п. |
1.2 |
Материал детали обладает литейными свойствами и в то же
время хорошо обрабатывается давлением, следовательно выбор процесса и метода
изготовления заготовки связан с обеспечением данного качества детали, т.е. с
техническими условиями на изготовление.
3. Выбор способа формообразования заготовки
Правильно выбрать заготовку - значит определить ее
пригодность для изготовления детали с позиций прочностных и стойкостных
характеристик, установить рациональный способ ее получения, определить
оптимальные припуски на обработку ее поверхностей, рассчитать размеры заготовки
и установить допуски на точность их выполнения, сконструировать заготовку и
разработать оптимальные технические условия на изготовление.
Основными факторами, учитываемыми при выборе заготовки,
являются:
масштаб и серийность выпуска (тип производства);
тип и конструкция детали (форма и размеры);
назначение детали в машине, материал и технические
условия на изготовление;
планируемые сроки на технологическую подготовку
производства;
конкретные условия производства (вооруженность завода и
кадры);
экономичность заготовки, выбранной с учетом предыдущих
факторов.
Все способы получения заготовок определяются:
1. Технологической характеристикой материала, т.е. его
литейными свойствами или способностью претерпевать пластические деформации при
обработке давлением, а такие структурными изменениями материала, получаемыми в
результате применения того или иного метода выполнения заготовки (расположение
волокон в прокате, поковках и штамповках, величина зерна в отливках и т.д.).
2. Конструктивными формами и размерами заготовки
(например, чем крупнее деталь, тем дороже обходится изготовление штампа, модели
или металлической формы).
3. Требуемой точностью выполнения заготовки и качеством
поверхности.
4. Величиной программного задания (при больших партиях
выгодны те способы изготовления заготовок, которые обеспечивают наибольшее
приближение формы и размеров заготовки к форме и размерам готовой детали).
5. Производственными возможностями заготовительных цехов
предприятия (наличием соответствующего оборудования).
6. Временем, затрачиваемым на технологическую подготовку
производства заготовок (на изготовление штампов, моделей, прессформ,
нестандартного оборудования и т.п.).
Выбор рациональной заготовки имеет важное экономическое
значение для получения высоких технико-экономических характеристик заготовительных
цехов и в целом для производства машин.
Рассмотрим несколько возможных способов формообразования
заготовки детали «Рычаг» и примем наиболее рациональный из них.
Опытно-технологические разработки по изготовлению рычагов
способами точного литья или сварки предварительно сформированных ковкой ступицы
и пальца не позволили получить необходимую прочность рычагов для крупных
гидротурбин. Поэтому примем к рассмотрению следующие способы:
-ковка с использованием подкладных штампов;
-отливка.
Способ изготовления рычага путем ковки с использованием
подкладных штампов.
Рычаг представляет собой одну из самых ответственных и
сложных по своей конфигурации деталей гидротурбины. Воспринимая усилие,
необходимое для разворота лопасти и определяемое гидродинамическим моментом,
рычаг одновременно подвержен воздействию знакопеременной нагрузки из-за
пульсации потока. Для изготовления рычага выбирают материалы, обеспечивающие
предел текучести 55—60 кгс/мм2 в сечениях 200—400 мм. Способ формообразования
заготовок рычага должен обеспечивать высокую плотность и однородность
материала, свободного от внутренних дефектов. При изготовлении поковок
необходимо, чтобы ось заготовки приблизительно совпадала с осью слитка, а
внешние очертания заготовки соответствовали наружным очертаниям рычага с учетом
напусков и припусков на механическую обработку.
Эксцентричность выступа (пальца) по отношению к диску, имеющему
расположенное в центре отверстие, создает ряд существенных трудностей при ковке
рычагов. Технологический процесс изготовления поковок рычагов осуществляется за
три нагрева под прессом с усилием 3000 тс (ковка заготовки) и прессом с усилием
10 000 тс (штамповка рычага). Для максимального приближения контура заготовки к
контуру готовой детали заключительные операции формообразования выполняют на
специальном штампе. После нагрева слитка до 1230° С проводятся закатка и
обрубка излишка цапфы и биллетировка слитка, после второго нагрева — осадка
слитка, требуемая для обеспечения необходимой плотности металла, протяжка и
обжатие конца на конус. После обрубки заготовки в меру она загружается в печь.
После третьего нагрева заготовку устанавливают выступом в отверстие штампа. Для
лучшего заполнения штампа оттянутому конусному концу придается необходимый
изгиб. Заготовку полностью осаживают верхней плитой, а разгонкой металла бойком
добиваются сплошности заполнения полости штампа. После прошивки отверстия
специальным прошивнем поковку выбивают из штампа и отправляют на
термообработку.
Таблица 6. Схема изготовления поковки рычага
Операции и переходы |
Эскизы переходов |
Первый нагрев (1230˚С) Закатка
цапфы и обрубка ее излишка биллетировка слитка |
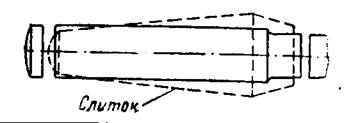
|
Второй нагрев (1230˚С) |
осадка слитка |
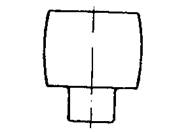
|
подсечка |

|
обжатие донного конца обрубка |

|
Третий нагрев (1230˚С) |
Оттяжка пальца |
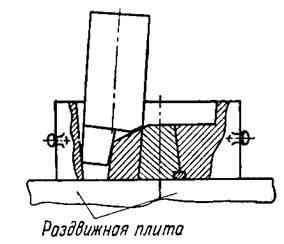
|
Осадка заготовки в штампе прошивка
отверстия |
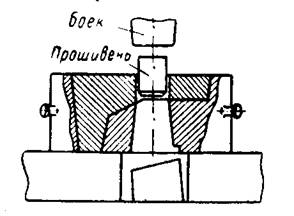
|
Готовая поковка |
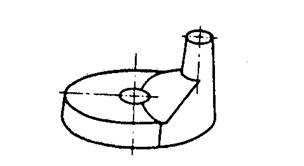
|
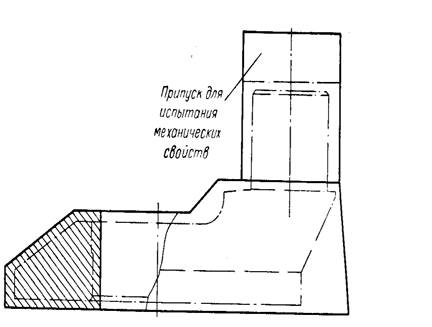
Рис. 2 Эскиз кованой заготовки рычага
При описанном технологическом процессе коэффициент
использования материала (по отношению к чистой массе) составляет: а) по черной
массе — 0,5—0,65; 6) по слитку — 0,35—0,4. Для получения требуемого уровня
механических свойств поковку подвергают термической обработке, режим которой
устанавливается предприятием-поставщиком заготовки.
При этом изготовление сложных штампов под крупные
заготовки также требует значительного расхода высокосортной стали, что также
является существенным недостатком данного способа, учитывая низкую степень
унификации рабочих колес гидротурбин.
В связи с высокой ответственностью рычагов их кованые за
готовки относят к пятой группе испытаний, предполагающей индивидуальную приемку
каждой поковки.
Изготовление рычагов свободной ковкой без использования
подкладных штампов еще более затратно, т.к. в этом случае коэффициент
использования металла не превышает 0,3.
Отливки получили широкое распространение во всех сферах и
отраслях промышленности благодаря возможности получения деталей практически
любой сложной геометрической формы из любых сплавов с внутренними полостями,
что практически невозможно получить другими способами, как ковка, сварка.
Отливки имеют большую степень конфигуративной точности и максимально приближены
к деталям. Суммарная энергоемкость при изготовлении деталей из литых заготовок
минимум в 2 раза меньше, чем при использовании других технологий.
Способ изготовления рычага литьем в песчаные формы
Распространенным способом производства литья является
способ литья в песчаные формы (песчано-глинистые, жидкие самотвердеющие смеси
(ЖСС), холоднотвердеющие смеси (ХТС) и др.). При этом способе в разовую
подготовленную форму производится заливка жидкого металла. После затвердевания
и охлаждения отливки форма разрушается. В зависимости от вида применяемых
формовочных смесей и противопригарных красок обеспечивается различное качество
отливок (по поверхности, внутренним дефектам, по отклонениям габаритных
размеров и пр.). Несмотря на значительный расход формовочных материалов - до 3
т на 1 т отливок - данный способ наиболее распространен в литейном
производстве, так как обеспечивает наибольшую универсальность и простоту
формообразования. Наиболее всего данный процесс применим для индивидуального и
мелкосерийного производства. Применяемые ЖСС и песчано-глинистые смеси
обеспечивают хорошее качество отливок, получаемых из чугуна и стали.
Так как минимальный диаметр d отверстия, получаемого с
помощью стержня, равен 6…10 мм при длине несквозного отверстия до 5d и
сквозного отверстия до 10d, следовательно в отливке можно получить 2 отверстия расположенных
на плоской ступице, что позволит повысить коэффициент использования металла и
снизить количество механической обработки. Исходя из вышесказанного, отливка
необходимой конфигурации получается с использованием 3 стержней.
Разработку технологического процесса изготовления отливки
начинают с анализа технологичности конструкции детали.
Технологичной называют такую конструкцию изделия или
составных ее элементов (деталей, узлов, механизмов), которая обеспечивает
заданные эксплуатационные свойства продукции и позволяет при данной серийности
изготовлять ее с наименьшими затратами. Технологичная конструкция
характеризуется простой компоновки, совершенством форм. Конструкция отливки
должна обеспечить удобство извлечения модели из формы, что достигается наименьшем
количеством разъемов модели, отъемных частей и стержней.
Деталь «Рычаг» имеет конфигурацию средней сложности (2
группа сложности) и обладает достаточно хорошей технологичностью для
изготовления ее способом литья. Минимальное и максимальное значение толщины
стенок отливки равны соответственно 200 и 247,5 мм. Конфигурация и расположение
поверхностей, подвергаемых обработке, полостей удовлетворяют основным
требованиям литейной технологии. При изготовлении отливки целесообразно
использовать прибыли, т.к. имеются тепловые узлы. Для выполнения полостей
необходимо использовать стержни.
Определение размеров опок и выбор их из стандартного
ряда.
Для отливки «Рычаг», габаритные размеры которой
1105х980х555 мм, экономичнее и целесообразнее взять опоку с габаритными
размерами из стандартного ряда опок в соответствии с ГОСТ 2133-75:
Верхняя полуформа: 1400х1100х400 мм
Нижняя полуформа: 1400х1100х350 мм
Определение размерной точности отливки и величину
припусков на механическую обработку производим в соответствии с требованиями
ГОСТ 26645-85. Припуски на механическую обработку устанавливают в зависимости
от допусков размеров отливок дифферецированно для каждого элемента. Для верхних
частей отливки предусматривают больший припуск на механическую обработку так
как там образуется неметалические включения.
1. Класс размерной точности отливки: Наибольший
габаритный размер отливки 1105 мм. Тип сплава термообрабатываемая сталь. Технологический
процесс- литьё в песчано-глинистые сырые формы из смесей с влажностью от 2,8 до
3,5% и прочностью от 120 до 160 кПа со средним уровнем уплотнения до твёрдости
не ниже 80 единиц. Класс точности отливки 10
2.Допуски размеров отливки:
Таблица 7
Номинальный размер, мм |
Допуск размера, мм |
Æ 250 |
3,6 |
Æ 980 |
5,0 |
Æ 485 |
4,4 |
555 |
4,4 |
200 |
3,6 |
Æ 115 |
3,2 |
3. Степень точности поверхности отливки:
Степень точности поверхности отливки 14
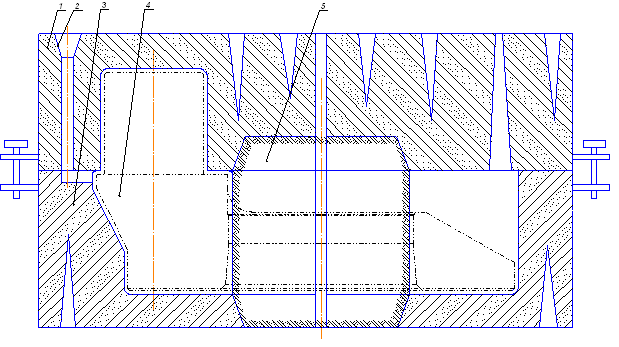
Рис. 3 Песчаная разовая форма в сборе: 1-верхняя
полуформа, 2-литниковая система (литниковая чаша и стояк), 3- нижняя полуформа,
4-отливка, 5- стержень.
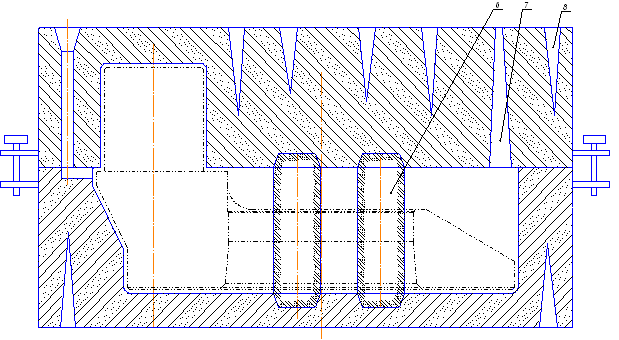
Рис. 4 Песчаная разовая форма в сборе (центральный
стержень условно не показан): 6-стержни (образующие два отверстия по сечению
Г-Г), 7- выпор, 8- вентиляционные отверстия.
Полуформы верхняя (поз. 1) и нижняя (поз.3) изготовлены
из песчано-глинистой смеси в металлических рамках (опоках). В полуформах с помощью
модели образована рабочая полость для получения отливки. Отверстия в отливке
образуют песчаные стержни (поз. 5,6), которые прочно скреплены с формой с
помощью стержневых знаков.
Полуформы перед заливкой скрепляют штырями. Для удаления
газов, выделяющихся из песчано-глинистой смеси и расплава, при заливке в форме
и стержне выполняют вентиляционные каналы (поз. 8). Расплав в рабочую полость
формы заливают через литниковую систему (поз. 2) — совокупность каналов, предназначенных
для подвода расплава в полость формы и питания отливки при затвердевании.
Назначение режимов термической обработки
Термическая обработка является обязательной операцией в технологическом
процессе производства стального литья.
Цель термообработки заключается в том, чтобы путем
нагрева до определенной температуры, некоторой выдержке при этой температуре и последующего
охлаждения изменить структуру стальных отливок, и получить необходимые свойства
прочности , пластичности, износоустойчивости, обрабатывающие или особые
прочностные свойства.
ТО отливки детали «Рычаг»:
нормализация 870-890oC с отпуском 570-600oC .
При нормализации происходит полная фаза перекристаллизации,
обеспечивая измельчение зерна, смягчение стали и снятие литейных напряжений:
образуются структуры более тонкого перлита, чем при отжиге.
Отпуск заключается в нагреве ниже интервала превращений,
выдержке при этой температуре и последующем охлаждении. При отпуске применяют превращение
неустойчивых структур закалки в более устойчивые по схеме мартенсит-тростит-сорбит,
и как следствие, с изменением структуры изменяются механические свойства, а
также одновременно снимаются внутренние напряжения.
4. Технологический процесс механической обработки рычага
Особенность конструкции рычага обусловлена не только
кинематикой механизма поворота, но и ограниченностью пространства в полости
втулки рабочего колеса, что приводит к необходимости конструирования его в виде
фасонной детали со скосами. При анализе ответственных сопряжений было
установлено, насколько существенны перпендикулярность оси пальца к плоскости М
и соблюдение (с точностью 0,2 - 0,3 мм) заданного расстояния между осями
ступицы и пальца. Указанные требования обуславливают необходимость обеспечения
технологического процесса специальной оснасткой. Ниже рассмотрены основные
этапы технологического процесса механической обработки заготовки рычага,
поставляемой в неободранном состоянии.
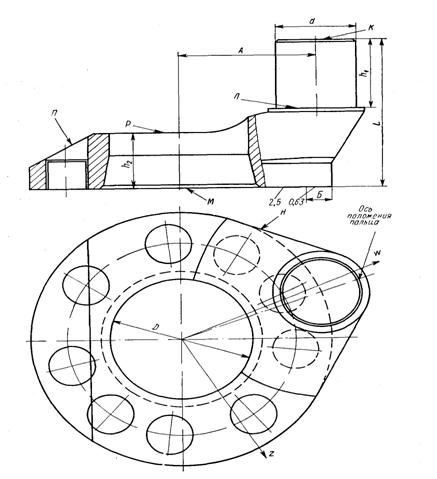
Рис. 5 Рычаг рабочего колеса
1. На разметочной плите производится расцентровка
заготовки, разметка осей пальца и центрального отверстия. Размечаются
поверхности К, Л, Р, М по высотным размерам h1, h2, L.
2. Деталь устанавливается на карусельном станке пальцем
кверху и выверяется по его оси. Отрезается припуск для пробы, из которой
изготавливаются образцы для испытания механических свойств. После испытания
образцов выдается заключение о годности детали и возможности ее обработки.
3. Выполняется карусельная обработка рычага, для чего
деталь устанавливают на подставки плоскостью М, совмещая ось пальца с осью
вращения планшайбы карусельного станка. Базой для установки служат высотные и
окружные риски разметки. Для исключения боя планшайбы из-за неуравновешенности
массы рычага на планшайбе, в месте, противоположном ступице, укрепляют
противовес. С припуском 5 мм подрезают торец пальца, точат поверхности d, Р и
конусную поверхность, соосную с пальцем рычага. Деталь кантуют, устанавливают
на проточенные кубари поверхностью Р и расцентровывают по риске разметки
поверхности В. Растачивают центральное отверстие и подрезают плоскость М с
припуском 5 мм.
4. Поверхность Н, необрабатываемая точением, фрезеруется
на поворотном столе.
5. Рычаг вновь устанавливают на мерные подставки план
шайбы карусельного станка пальцем вниз и выставляют по поверхностям М и В.
Растачивают окончательно центровое отверстие по 2-му классу точности и подрезают
торец. Для обеспечения необходимой шероховатости на участке Б поверхности М,
контактирующем с торцом бронзовой втулки корпуса рабочего колеса, указанный
участок обрабатывают шлифованием. После этого производят окончательную
обработку пальца рычага.
Требуемая точность межосевого расстояния А обеспечивается
технологически с помощью специального приспособления (рис. 6), на основании
которого имеется центрирующая втулка 2 и съемный установочный штырь 3.
Расстояние между осью штыря и втулки выдержано с точностью 0,1 мм.
Приспособление устанавливают на планшайбу 4 карусельного станка и
расцентровывают по цилиндрической поверхности штыря с помощью индикатора с
точностью 0,02 мм. После закрепления приспособления на планшайбе штырь удаляют
и рычаг устанавливают поверхностью В на центрирующую втулку и, разворачивая его
относительно вертикальной оси, добиваются равномерного припуска по
цилиндрической поверхности пальца.
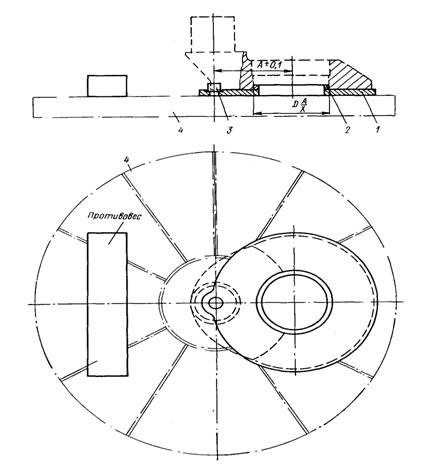
Рис. 6 Приспособление для обработки пальца рычага
В этом случае погрешность размера А будет находиться в
пре делах, определяемых соотношением
DА
= Dпр + Dш + Dвт
где Dпр
погрешность межосевого расстояния А приспособления; Dш — несоосность установочного штыря с осью
вращения планшайбы; Dвт
- половина зазора в сопряжении центрирующей втулки с отверстием D рычага.
6. Рычаг устанавливают на разметочной плите вертикально,
выверяя поверхность М (см. рис. 5.23) по угольнику таким образом, чтобы центры
О и 0 находились в одной горизонтальной плоскости. Наносят базовую риску — ось
положения пальца, перенося ее на поверхность М. С помощью зеркального кондуктора
(того же, что использовался при разметке отверстий во фланцах лопасти и цапфы)
размечают на поверхности М с выносом на образующую оси z и w. Размечают
положение осей отверстий под болты и шпонки и дают риски обработки скосов по
плоскости П.
7. На строгальном станке обрабатывают скосы одновременно
для всего комплекта рычагов. детали выставляют по ходу стола и выверяют по
рискам разметки.
8. На станке КУ-11 растачивают и нарезают отверстия под
болты. Отверстия под шпонки растачивают с припуском 5 мм для совместной
обработки с лопастью и цапфой.
9. Для увеличения прочности наиболее нагруженного сечения
в месте перехода пальца рычага к диску производят наклеп галтели с помощью
приспособления (рис. 5), надеваемого на палец рычага. Технология наклепа и
оснастка разработаны ЦНИИТмашем. На корпусе 1 крепится пневматический молоток
2, устанавливаемый под углом 55˚ к оси пальца рычага. Ударный импульс
передается ролику 3, радиус торовой поверхности которого равен 5 мм. В процессе
наклепа приспособление проворачивается вокруг оси пальца, подвергая
поверхностному пластическому деформированию галтель по всей окружности. Наклеп
производится за два прохода при скорости вращения приспособления 1,5—2 об/мин.
Частота импульсного воздействия ролика примерно 2000 ударов в минуту.
Оценка достигнутого уровня упрочнения осуществляется
путем измерения деформации зоны галтельного перехода. Измерение проводится в
направлении деформирующего усилия с по мощью индикатора, устанавливаемого в
приспособление, конструкция которого аналогична описанному выше.
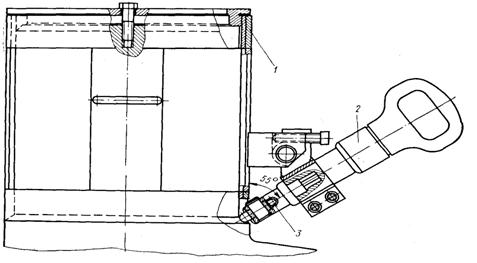
Рис. 7 Приспособление для наклепа галтели рычага
Использованная литература
1.
Броновский Г.А, Гольдфарб А.И., Фасулати Р.К. Технология
гидротурбиностроения Л:«Машиностроение», 1978 г.
2.
ГОСТ 26645–85. Отливки из металлов и сплавов. Допуски размеров, массы и
припуски на механическую обработку
3.
Грановский С.А., Орго В.М. Конструкция и расчет гидротурбин
4.
«Машиностроение», 1974г.
5.
Ковалев Н. Н. Проектирование гидротурбин «Машиностроение», 1974г.
6.
Михайлов А. М. и др. Литейное производство: Учебник для металлургических
специальностей вузов. – М.: Машиностроение, 1987.
7.
Орго В.М. Гидротурбины «Издательство Ленинградского университета, 1975
г.
8.
Рихтер Р. Конструирование технологичных отливок. – М.: Машиностроение,
1968. – 254 с.
9.
Шварцбурд Б.И. Технология производства гидравлических машин. - М:
«Машиностроение»,1978 г.
|