Промышленность производство : Дипломная работа: Проектирование кислородно-конвертерного цеха №2 ОАО "ММК"
Дипломная работа: Проектирование кислородно-конвертерного цеха №2 ОАО "ММК"
1
ОБОСНОВАНИЕ
ПРОЕКТА СТРОИТЕЛЬСТВА
КИСЛОРОДНО-КОНВЕРТЕРНОГО
ЦЕХА №2 ОАО «ММК»
1.1
Общая
характеристика комбината
1.1.1
Сырьевая
база предприятия
Снабжение
железорудным сырьем ОАО «ММК» в настоящее время сориентировано на привозные
руды и руды местных месторождений. Потребность ММК в железорудном сырье
составляет около 14 млн.т/год. Сырьевой базой ММК на ближайшее время остается
рудник Малый Куйбас (общий объем добываемого сырья равен 1,5 млн.т сырой руды в
год), рудник горы Магнитной, Качканарское и Лисаковское месторождения. Мощность
горно-обогатительного комбината близ Лисаковского месторождения составляет
около 35 млн. т/год исходной руды с содержанием железа 47,5 %.
Другим немаловажным
источником получения местного сырья являются отвальные шлаки, которых
насчитывается около 150 млн. т. В шлаках ММК содержится до 30 % железа.
Снабжение
известняком ММК осуществляется с Агаповского месторождения (промышленные запасы
известняка около 100 млн.т). В год добывается около 420 тыс. т сырого
известняка. В зависимости от содержания основных компонентов различают три
сорта известняков, состав которых приведен в табл. 1.1.
Таблица 1.1
Состав известняка
Компоненты
|
Содержание, %
|
1 сорт |
2 сорт |
3 сорт |
CaO+MgO (не менее) |
53,5 |
53,0 |
53,0 |
в т.ч. MgO (не более) |
3,5 |
7,0 |
16,0 |
Al2O3 (не более) |
3,0 |
3,0 |
3,0 |
RO2 (не более) |
2,0 |
2,5 |
2,5 |
Снабжение ММК доломитом
осуществляется с Лисьегорского месторождения, промышленные запасы доломита которого
составляют около 31 млн.т. Огнеупорная глина доставляется с Южно-Уральского
рудника (промышленные запасы глины около 435 млн. т). Подготовка флюсовых
материалов производится на базе Агаповского месторождения известняка.
В составе
горно-обогатительного производства ММК эксплуатируются:
- дробильно-сортировочная
фабрика № 2;
- дробильно-обогатительная
фабрика № 5;
- агломерационные фабрики
2, 3, 4 с общей площадью спекания 898,5 м2.
В состав
известняково-доломитового производства входят:
- горный цех, объединяющий
известняковый и доломитовый карьеры;
- дробильно-сортировочная
фабрика;
- известняково-обжиговая
фабрика № 1 с двумя вращающимися печами и дробильным отделением;
- известняково-обжиговая
фабрика № 2 с печью КС-1200, производящая известь для кислородно-конвертерного
цеха;
- известняково-обжиговая
фабрика № 3, в состав которой входят дробильно-сортировочная фабрика и шахтные
печи по обжигу известняка и доломита.
Коксохимическое
производство ММК имеет в своем составе:
- углеподготовительный цех;
- три коксовых цеха (семь
коксовых батарей);
- цех улавливания
химпродуктов № 1 и 2;
- смолоперерабатывающий цех
(введен в эксплуатацию в 1980 г. и имеет общее производство 315 тыс. т/год);
- химустановку
(биохимочистку).
Огнеупорное производство
ММК включает:
- шамотный цех № 1 (введен
в 1935 г.), морально и физически устаревший;
- шамотный цех № 2 (введен
в 1965 г.) с шамотно-обогатительной установкой, состоящий из двух вращающихся
печей и участков вспомогательного назначения;
- участок переработки
огнеупорного лома (введен в 1987 г.), где на установке по переработке
огнеупорного лома ежегодно перерабатывается 110…120 тыс. т огнеупоров, из
которых 60…70 тыс. т отбирается для дальнейшего использования [6].
1.1.2
Топливно-энергетические
ресурсы
В настоящее время на ММК
основным источником получения газообразного топлива являются доменные печи и
коксовые батареи. Снабжение природным газом осуществляется от областного
газопровода.
Основным потребителем
кислорода на ММК являются доменный, кислородно-конвертерный, и мартеновский
цеха. Снабжение кислородом осуществляется от кислородных станций № 4 и 5.
Подача аргона и азота
осуществляется от кислородной стации № 5. Для подачи кислорода, азота и аргона
в ККЦ № 2 ММК необходимо будет строительство новых трасс трубопроводов.
Обеспечение сжатым
воздухом кислородно-конвертерного цеха № 2 планируется от Восточной
компрессорной. Однако, в связи с тем, что ряд потребителей конвертерного цеха
предъявляет жесткие требования к качеству воздуха (точка росы не выше –400С)
необходимо будет пристроить к компрессорной установку осушки воздуха
производительностью 1500 м3/мин.
Питание электрических
нагрузок Магнитогорского промузла, в настоящее время, осуществляется от
Магнитогорских тепловых станций, от ПС 500/220 кВ «Магнитогорская-1» и
«Магнитогорская-2» («Смеловская»), а также по двум ВЛ-220 кВ от Троицкой ГРЭС. Электроснабжение
всех промышленных предприятий города и жилого фонда осуществляется через
подстанции и электрические сети ММК, поэтому развитие схемы электроснабжения
ММК тесно связаны с развитием Магнитогорского промузла в целом [7].
Источником
производственного водоснабжения ММК является река Урал. Подача воды
осуществляется из заводского пруда насосными станциями. Существующее
водопотребление ММК в 1995 г. составляет 344950 м3/ч, в том числе безвозвратные
потери – 12307 м3/ч (3,42 м3/с). Общий годовой расход воды составил 2996244
тыс.м3 [6].
Покрытие безвозвратных
потерь воды промрайона в маловодный год 95 % обеспеченности может быть
осуществлен за счет водоотдачи существующих Верхне-Уральского и Магнитогорского
водохранилищ, а также использования повторно доочищенных сточных вод
хозяйственно-бытовой канализации очистных сооружений правого и левого берега г.
Магнитогорска.
Береговые насосные
станции № 9, 9а, 1, 1а, 17, 16, 16а, 12 полностью обеспечат подачу свежей воды
на покрытие безвозвратных потерь систем оборотного водоснабжения цехов ММК и
цехов, работающих на прямоточной системе.
1.1.3
Основные
металлургические переделы
К
основным металлургическим переделам комбината относятся доменное,
сталеплавильное и прокатное производства.
В
доменном цехе из 10 печей, в настоящее время, в работе находится 7 доменных
печей (№ 2, 4, 6, 7, 8, 9, 10) суммарным объемом 10810 м3. Производство
передельного чугуна на ММК в 2001г. составило около 8000 тыс. т [7].
В
состав сталеплавильного производства ОАО «ММК» входят мартеновский и
кислородно-конвертерный цеха. В мартеновском цехе выплавка стали осуществляется
в мартеновских печах № 26, 27, 28 и на двухванных сталеплавильных агрегатах (
29 и 32). В мартеновском цехе выплавляются спокойная, кипящая, полуспокойая,
низколегированная, легированная, автоматная и высококачественная марки стали.
За 2001 г. производство стали в мартеновском цехе ММК составило 2427829 т.
Кислородно-конвертерный
цех № 1 ОАО «ММК» включает в себя: три конвертера вместимостью по 370 т, две
установки доводки стали, одну установку комбинированного вакуумирования стали и
одну установку типа «печь-ковш». Цех также имеет четыре слябовые машины непрерывного
литья заготовок (МНЛЗ). Получаемая заготовка имеет сечение 250 х (750…2350) мм.
Всего в ККЦ № 1 за 1999 г. было произведено 6616056 т слябовых заготовок из
стали следующего сортамента: углеродистой обыкновенного качества – 15,65 %;
углеродистой качественной конструкционной – 39,52 %; автокузовной – 36,36 %;
низколегированной – 3,84 % и легированной – 4,63 % [22]. Производство стали в
ККЦ в 2001г. составило около 7,9 млн. т.
Сортопрокатное
производство ММК в настоящее время представлено обжимно-заготовочным цехом (ОЦ
2 – блюминг) и сортовым цехом, объединившим проволочно-штрипсовый и
сортопрокатный цеха. В состав сортового цеха входят:
-
проволочный
стан 250-2 (введен в 1938 г.);
-
мелкосортный
стан 250-1 (введен в 1935 г.);
-
среднесортный
стан 300-1 (введен в 1935 г.);
-
крупносортный
стан 500 (введен в 1934 г.);
-
штрипсовый
стан 300-2 (введен в 1935 г.).
Все
сортовые станы ММК морально и физически устарели.
В
составе листопрокатного производства ММК в настоящее время имеются:
-
стан
2500 горячей прокатки (введен в 1960 г.), поставляющий прокат для стана 2500
холодной прокатки, цеха гнутых профилей, цеха ленты и цеха жести;
-
стан
2000 горячей прокатки (введен в 1994 г.);
-
цех
жести (ЛПЦ-3);
-
цех
покрытий (ЛПЦ-6);
-
цех
углеродистой ленты (ЛПЦ-8);
-
цех
гнутых профилей (ЛПЦ-8).
1.1.4
Утилизация
отходов и экономическая обстановка
С
учетом требований технологии и опыта эксплуатации отечественных и зарубежных
цехов в планируемом ККЦ предусмотрены наиболее передовые технические решения по
улавливанию и очистке технологических газов и неорганизованных выбросов.
Полное
укрытие конвертера с индивидуальным отводом газов от укрытия на центральную
газоочистную станцию с рукавными фильтрами, позволяет эффективно улавливать
неорганизованные выбросы от конвертера, образующиеся при завалке металлолома,
заливке чугуна, выпуске металла и сливе шлака. Применение рукавных фильтров
обеспечивает нормальные условия труда в конвертерном отделении [1].
Улавливание
и очистка неорганизованных выбросов до санитарных норм в двухступенчатых
газоочистках предусмотрено также при выполнении следующих технологических
операций:
-
при
переливе чугуна из миксерных ковшей;
-
при
скачивании шлака из заливочных ковшей;
-
при
перегрузке сыпучих материалов и ферросплавов по тракту;
-
при
внепечной обработке металла на агрегатах доводки;
-
при
порезке заготовок на машинах газовой резки.
Для
обеспечения цеха водой заданных параметров по качеству и создания бессточной
системы водоснабжения сооружено четыре оборотных цикла: «грязные» циклы
газоочисток и МНЛЗ, циклы установки вакуумирования и оборудования цеха.
Технические
решения по безотходности технологии включает:
-
утилизация
шламов от газоочисток конвертера и МНЛЗ;
-
использование
пара, вырабатываемого в котлах-охладителях на нужды цеха;
-
переработку
конвертерных шлаков с извлечением из них металла и получением
фракционированного щебня и гранулированного шлака;
-
использование
конвертерного газа в качестве топлива;
-
использование
отсеиваемой мелочи извести для приготовления шлакообразующих смесей, а также в
агломерационном производстве;
-
переработку
огнеупорного боя для вторичного использования в огнеупорном производстве и для
нужд восстановления изношенной футеровки агрегатов.
В
настоящее время на ММК имеется отвальный шлак в количестве 150 млн. т и шлак
текущего производства – доменный, мартеновский и конвертерный. Для переработки
шлака действуют следующие установки:
1.
По переработке доменных шлаков текущего производства:
- гидрожелобная
грануляционная установка треста «Магнитострой» мощностью 1500 тыс. т/год
граншлака;
- бассейновая
грануляционная установка треста «Магнитострой» мощностью 270 тыс. т/год легкого
граншлака;
- шлакопемзовая струйная
установка треста «Магнитострой» мощностью 150 тыс м3/год шлаковой пемзы;
- барабанная грануляционная
установка цементного завода мощностью 1000 тыс. т/год граншлака;
- три траншеи для приема
скардовин длиной по 160 м.
2.
По переработке отвальных доменных шлаков, где переработка осуществляется на
дробильно-сортировочных комплексах (ДСК) мощностью 1,2 млн. т/год.
3.
По переработке шлаков текущего мартеновского производства:
- шлаковые дворы № 1 и 2;
- эстакада разгрузки
шлаков;
- две передвижные установки
SKJ (Финляндия).
4.
По переработке шлаков конвертерного производства:
- участок первичной
переработки;
- установки СП
«Трейдметинвест» мощностью 2,4 млн. т/год.
Магнитогорский
металлургический комбинат является крупнейшим производителем проката для
различных предприятий Южно-Уральского региона. В их числе находится немало
ведущих предприятий метизной промышленности, таких как: Магнитогорский
калибровочный завод, Магнитогорский метизно-металлургический завод, Белорецкий
металлургический комбинат, УралАЗ и др. Производство сортового проката на ММК в
настоящее время находится на уровне 2,0 млн. т/год. Однако, ожидаемый в течение
ближайших лет подъем отечественной экономики, сопровождаемый модернизацией
существующих и строительством новых промышленных предприятий, несомненно
приведет к резкому повышению спроса на сортовой прокат. Поэтому необходимо
планировать развитие сортопрокатного производства ММК, с тем чтобы иметь
возможность удовлетворять повышенный спрос на сортовой прокат [7].
В настоящее время металл
на ММК для сортового проката выплавляется в мартеновском цехе № 1 с разливкой
стали в изложницы. Такое производство устарело морально и физически. Поэтому
мартеновский цех в ближайшем будущем будет выводиться из эксплуатации.
Следовательно, комбинату необходимо срочно решать проблему выплавки стали для
сортопрокатного производства.
Получать
металл для сортового проката в существующем конвертерном цехе ММК не
представляется возможным по следующим причинам. Все машины непрерывного литья
заготовок в цехе предназначены для отливки слябов. Установка же дополнительно
одной или двух МНЛЗ для отливки сортовой заготовки приведет к тому, что:
- для разливки
370 т металла на сортовой МНЛЗ потребуется значительно больше времени, чем для
разливки на слябы; следовательно, возникнет проблема синхронизации работы
конвертерного отделения и отделения непрерывной разливки стали (ОНРС), особенно
при организации работы МНЛЗ сериями (методом «плавка на плавку»);
- при
установке в цехе дополнительных сортовых МНЛЗ придется увеличить объем
выплавляемой стали, чтобы обеспечить металлом как листо- так и сортопрокатное
производство с организацией двух независимых грузопотоков металла – слябы и
блюмы;
- наличие в цехе
разнотипных машин существенно усложнит организацию их ремонтов со снабжением
сменным оборудованием.
Таким
образом, на Магнитогорском металлургическом комбинате неизбежно создание новой
технологической линии по производству сортовых заготовок. Производительность
этой линии желательно иметь на уровне 3,0 млн. т. Для этого может быть принят
кислородно-конвертерный цех с двумя конвертерами вместимостью 200 т,
работающими по классической схеме (один в работе, другой на ремонте или в
резерве). Для получения металла, отвечающего требованиям мировых стандартов,
цех должен иметь отделение непрерывной разливки стали с участками ковшевой
обработки и разливки.
В основу
стратегии развития ММК закладывается решение следующих задач:
- повышение
эффективности работы комбината и рентабельности производства;
- внедрение
современных ресурсо- и энергосберегающих технологических процессов;
- достижение
конкурентоспособности металлопродукции на внутреннем и внешних рынках;
- создание
новых рабочих мест;
- внедрение
современных форм управления и организации труда;
- улучшение
условий труда;
- улучшение
экологической обстановки.
Поддержание в
работе устаревшего оборудования за счет капитальных ремонтов, а также
незначительные реконструкции отдельных агрегатов не могут привести к выигрышу в
долговременной конкурентной борьбе за рынки сбыта и обеспечить решение
вышеперечисленных задач. Этого можно добиться лишь за счет коренного
технического перевооружения и новых технологий.
1.2
Вариант
строительства ККЦ № 2 ММК
Кислородно-конвертерный
цех № 2 ОАО «ММК» предполагается строить на площадке перед имеющимся сортовым
станом блюминга № 3. Это позволит значительно сократить время транспортировки
горячих блюмов из ОНРС до сортового стана. Также это позволяет объединить
объекты подсобного и обслуживающего назначения (электроподстанцию,
компрессорную, котельную и др.) с работающим блюмингом.
2
УСТРОЙСТВО
И ОБОРУДОВАНИЕ ЦЕХА
2.1
Выбор
основного оборудования
В кислородно-конвертерном
цехе № 2 для выплавки 3,0 млн. т стали в год, устанавливаются:
-
два
кислородных конвертера вместимостью 200 т каждый, работающих по классической
схеме;
- одна установка
вакуумирования стали циркуляционного типа;
- одна двухпозиционная
установка типа «печь-ковш»;
- четыре шестиручьевые МНЛЗ
криволинейного типа для получения заготовок квадратного сечения 250 х 250 мм.
Бесперебойная работа цеха
обеспечивается установкой следующего кранового оборудования:
-
заливочные
краны;
-
разливочные
краны;
-
краны
для перестановки ковшей в отделении перелива чугуна;
-
краны
для перестановки совков со скрапом;
-
краны
для перестановки шлаковых чаш в шлаковом пролете.
Кроме того, устанавливается
следующее технологическое оборудование:
-
ковши
миксерного типа;
-
сталеразливочные
ковши;
-
совки
для скрапа;
-
шлаковые
чаши;
-
машина
«Орбита» для ломки футеровки;
-
стенд
для выкладки футеровки;
-
стенды
для сушки футеровки [23].
2.2
Структура
и планировка цеха
Основные планировочные и
технические решения приняты с учетом размещения цеха на новой промышленной
площадке комбината и максимального использования установившихся схем
обеспечения энергоресурсами и материалами, а также эксплуатации уже имеющихся
вспомогательных объектов и сооружений.
Конвертерный цех
представляет собой комплекс технологически связанных производственных
отделений, пролетов и участков с установленным в них технологическим,
подъемно-транспортным, вспомогательным и ремонтным оборудованием, которое
необходимо для обеспечения намеченного объема производства цеха.
Конструктивно
конвертерный цех № 2 ОАО «ММК» состоит из следующих отделений [19]:
-
конвертерное
отделение (КО);
-
отделение
непрерывной разливки стали (ОНРС);
-
транспортно-отделочное
отделение (ТОО).
В свою
очередь, конвертерное отделение в себя включает:
-
отделение
перелива и десульфурации чугуна;
-
скрапное
отделение;
-
пролет
перестановки шлаковых чаш;
-
пролет
постов управления и электропомещений;
-
загрузочный
пролет;
-
конвертерный
пролет;
-
пролет
подготовки и ремонта сталеразливочных и промежуточных ковшей;
-
участок
сыпучих материалов и ферросплавов.
ОНРС включает
в себя:
-
пролеты
МНЛЗ;
-
участок
вакуумирования стали;
-
участок
доводки металла в ковше;
-
пролет
подготовки технологического оборудования;
-
пролеты
электропомещений для МНЛЗ.
ТОО включает:
- транспортно-отделочную
линию (ТОЛ);
-
участок
выборочной зачистки блюмов;
-
участок
ручной зачистки блюмов.
Ремонт
футеровки конвертера осуществляется в специальном пролете, прилегающем к
конвертерному. Подача огнеупоров в пролет ремонта сталеразливочных и
промежуточных ковшей предусмотрена на автотранспорте.
3
ПРОИЗВОДСТВЕННАЯ
СТРУКТУРА
ОТДЕЛЕНИЯ КОВШЕВОЙ
ОБРАБОТКИ СТАЛИ
3.1
Организация
грузопотоков
Основными грузопотоками в
отделении ковшевой обработки является грузопоток жидкой стали и грузопоток
сыпучих и ферросплавов.
Доставка
жидкого металла в отделение ковшевой обработки осуществляется в
сталеразливочных ковшах на самоходных сталевозах. Далее, с помощью разливочных
кранов ковши с металлом передаются на сталевозы агрегата «печь-ковш», либо
вакууматора. После обработки ковши транспортируются в ОНРС с помощью
разливочных кранов грузоподъемностью 280+100/20 т [см.прил.1].
Сыпучие,
кусковые материалы и ферросплавы подаются в отделение ковшевой обработки стали
по конвейерному тракту из бункеров отделения приема сыпучих и ферросплавов.
Перед непосредственной загрузкой сыпучих и ферросплавов в ковш производится их
взвешивание с точностью ± 10 кг.
3.2
Организация
труда в отделении ковшевой обработки
и на главных рабочих
местах
Правильная организация
труда в отделении обеспечивает ритмичную работу и дает возможность поддерживать
объем производства на заданном уровне.
Режим работы
агрегатов в отделении ковшевой обработки - непрерывный. Работа
промышленно-производственного персонала, обслуживающего агрегаты, организуется
по четырех бригадному графику при непрерывной производственной неделе с
восьмичасовой рабочей сменой. Каждый агрегат обслуживают два оператора в смену.
Выбор
расположения рабочих мест осуществлен с учетом специфики и особенностей
размещения технологического оборудования, протяженности и оснащенности зон
обслуживания, условий труда, а также трудовых функций работающих.
Постоянные
рабочие места находятся в посту управления, расположенном на рабочей площадке.
Функции по
текущему обслуживанию оборудования, кроме технологического персонала,
возлагается на дежурный персонал проектируемого ККЦ (профилактический осмотр
оборудования, устранение мелких неисправностей, возникающих в процессе работы
оборудования, смазка узлов и механизмов, участие в выполнении ремонтных работ,
проводимых ремонтным персоналом цеха).
3.3 Организация ремонта
основного технологического оборудования
Ремонты оборудования
отделения ковшевой обработки стали осуществляются централизованно силами
специальных служб слесарей по ремонту и обслуживанию металлургического
оборудования комбината. Текущее обслуживание оборудования и механизмов
производится дежурным персоналом цеха, профилактический осмотр оборудования
по утвержденному начальником цеха графику. Периодичность осмотров оборудования
регламентируется правилами технической эксплуатации механического и
электрического оборудования. Результаты осмотров фиксируются в специальный
журнал. На основании этих данных подаются заявки в отделы главного механика и
энергетика о замене деталей или узлов оборудования. По устранению неполадок
делается соответствующая запись в журнале о выполнении работ. Работы по
межремонтному обслуживанию выполняются во время перерывов в работе
оборудования. Текущие, средние и капитальные ремонты производятся по
утвержденному на комбинате плану-графику.
Замена
водоохлаждаемого свода агрегата «печь-ковш» производится при помощи установленного
в отделении крана грузоподъемностью 20 т. Для ремонта изношенного свода
предусмотрен специальный стенд в непосредственной близости от агрегата [24].
Проведение
ремонта футеровки вакуумкамеры предполагается проводить на рабочем месте
вакууматора и на спецстенде. Для замены изношенной футеровки возможно
использование крана отделения ковшевой обработки и ремонтной тележки
вакуумкамеры [5].
Текущие,
средние и капитальные ремонты электрооборудования выполняются силами
централизованных служб главного энергетика.
3.4
Структура
управления отделением ковшевой обработки стали
Организационная
структура управления проектируемым отделением, представлена на рис. 3.1.

Рис. 3.1 Схема управления
отделением ковшевой обработки
4
КОВШЕВАЯ
ОБРАБОТКА СТАЛИ
На
современном этапе производства стали в кислородных конвертерах необходима ее
последующая ковшевая обработка. Внепечная обработка позволяет выплавлять в
конвертерах широкий сортамент легированных сталей, идентичных по качеству
металлу мартеновского и электропечного производств. Использование того или
иного вида внепечной обработки конвертерной стали должно рассматриваться исходя
из экономических соображений и применительно к каждому классу стали.
Удаление вредных примесей
из металла в плавильных агрегатах до требуемых значений экономически
нецелесообразно, а в ряде случаев и невозможно. При обработке же стали в
ковшах, создаются оптимальные условия для десульфурации, дефосфорации и
удаления неметаллических включений.
Методы внепечной
обработки стали могут быть условно разделены на простые (обработка металла
одним способом) и комбинированные (обработка металла несколькими способами). К
рассмотренным выше простым методам относятся:
- обработка металла
вакуумом;
- продувка инертным газом;
- обработка металла
синтетическим шлаком, жидкими или твердыми шлаковыми смесями;
- введение реагентов вглубь
металла.
Основными недостатками
перечисленных простых способов обработки металла являются: а) необходимость
перегрева жидкого металла в плавильном агрегате для компенсации падения
температуры металла при обработке в ковше; б) ограниченность воздействия на
металл (только десульфурация, только дегазация и т.п.).
Лучшие результаты
воздействия на качество металла достигаются при использовании комбинированных
или комплексных способов, когда в одном или нескольких последовательно расположенных
агрегатах осуществляется ряд операций. Одним из наиболее современных
комбинированных агрегатов является установка типа «печь-ковш».
Основные же способы
внепечного вакуумирования стали, применяющиеся в промышленном масштабе, обычно
делят на три группы: вакуумирование в ковше, струйное вакуумирование и
обработка металла вне ковша в специальной вакуумкамере. Однако, наибольшее
распространение, вследствие меньших потерь температуры металла при обработке,
меньшего количества сопутствующего оборудования (а следовательно - дешевизны) и
более качественных получаемых результатов, получил метод вакуумной обработки
металла порциями, а именно порционное (DH-процесс) и
циркуляционное вакуумирование стали (RH-процесс).
Вынесение части операций рафинирования из плавильного
агрегата на установку «печь-ковш» дает следующие преимущества:
-
повышается
производительность плавильного агрегата;
-
увеличивается
стойкость футеровки;
-
снижается
потребление энергоносителей.
Установки типа «печь-ковш» выгодно отличаются универсальностью,
гибкостью и высокими технологическими результатами.
Установка циркуляционного вакуумирования стали (УЦВС) перед
установкой порционного вакуумирования имеет ряд преимуществ, а именно – более
низкие капитальные затраты на строительство, отсутствие тяжелого и,
следовательно, дорогостоящего сопутствующего оборудования (гидравлики,
механизмов перемещения камеры и др.), а также меньшее время обработки плавки.
На УЦВС возможна обработка нераскисленной или полураскисленной конвертерной
стали, для производства нестареющего металла глубокой и особосложной вытяжки
(автолист, жесть и др.) [1, 27].
В проекте предусмотрена установка одного агрегата
«печь-ковш» и одной установки циркуляционного вакуумирования стали. Агрегаты
размещаются над дополнительным сталевозным путем, расположенном между
основными. Каждый агрегат обслуживается разливочным краном МНЛЗ того пролета,
где он расположен.
На агрегате «печь-ковш» осуществляются следующие
технологические операции:
-
нагрев
металла с помощью заглубленных электрических дуг;
-
продувка
металла инертным газом (аргоном);
-
рафинирование
под белым основным шлаком;
-
замер
температуры и отбор проб металла;
-
введение
в металл алюминиевой проволоки и присадка кусковых материалов (ферросплавов).
Ковшевой обработке на агрегате «печь-ковш» подвергаются
такие стали, как низколегированные трубного сортамента с содержанием серы не
более 0,005 % (типа 09Г2ФБ, 09Г2БТ), особонизкосернистые и
особонизкоуглеродистые (типа 09Г2С, 50ХГФА), низколегированные с содержанием
серы не более 0,010 % (типа 22Ю), нестареющая автолистовая сталь марки 08Ю, а
также все марки стали, температура которых не позволяет провести их обработку
на обычных агрегатах доводки стали [24].
Установка циркуляционного вакуумирования стали
предназначена для:
-
удаления
растворенных в металле газов (кислорода, водорода, азота);
-
углеродистого
раскисления стали (релейной, трансформаторной, динамной, автоматной) с
уменьшением содержания углерода до 0,010 %;
-
корректировки
по химическому составу;
-
корректировки
по температуре [25].
5
КОНСТРУКЦИЯ
И ОБОРУДОВАНИЕ
АГРЕГАТА «ПЕЧЬ-КОВШ»
Процесс обработки на
агрегате осуществляется в ковше с основной футеровкой, который закрывается
полностью водоохлаждаемым сводом. Подача электроэнергии осуществляется с помощью
трех графитовых электродов.
Агрегат имеет два
стенда, обслуживаемые одним трансформатором и одним комплектом электродов.
«Печь-ковш» включает в себя следующие группы оборудования, узлы и системы:
-
каркас
установки со встроенными помещениями поста управления и трансформатора;
-
система
хранения, дозирования и механизированной подачи сыпучих (ферросплавов);
-
тракт
подачи сыпучих;
-
трайб-аппараты
для ввода в металл алюминиевой проволоки;
-
две
водоохлаждаемые крышки сводов;
-
механизм
подъема сводов;
-
поворотный
электродный портал с графитовыми электродами;
-
трансформатор;
-
система
высокого тока (для передачи электроэнергии от трансформатора к электродам);
-
системы
для донной продувки;
-
две
аварийные верхние фурмы;
-
манипуляторы
для измерения температуры и отбора проб металла;
-
стенд
наращивания электродов;
-
два
сталевоза.
Применяемый на
проектируемом агрегате «печь-ковш» трансформатор имеет номинальную мощность
32,0 МВ*А, силу тока электрода 59,6 кА и диапазон вторичных напряжений 420…218
В [20].
Агрегат «печь-ковш»
размещается в пролете МНЛЗ № 3. Ширина пролетов машин – по 16 м (см. лист 1)
[18].
Для установки
«печь-ковш» характерны следующие отличительные конструктивные признаки [26]:
1.
Токопроводящие
консоли электродов:
-
токопроводящие
консоли электродов выполнены из медноплакированного стального листа и имеют
жесткую блочную конструкцию. Блочный профиль с интегрированными каналами
охлаждающей воды обеспечивает высокую прочность консолей, которая позволяет
высокую скорость регулирования;
-
компактная
конструкция токопроводящих консолей обеспечивает минимальный распад электродов
при максимально свободном пространстве;
-
основная
изоляция между консолью и подъемной стойкой с обеих сторон охлаждается водой;
-
через
контактную щеку электроды зажимаются в консоли с помощью тарелочных пружин.
Силу зажима можно ослабить с помощью гидравлического цилиндра. Вся система
интегрирована в консоль и тем самым защищена от электрического,
электромагнитного и теплового воздействия;
-
конструкция
консолей уменьшает реактанс и омическое сопротивление и позволяет максимально
использовать электрическую энергию;
-
электрические
консоли практически не требуют технического ухода.
2.
Конструкция
свода:
-
свод
установки «печь-ковш» является полностью водоохлаждаемым. Внешняя часть свода
выполнена в виде конструкции «труба в трубе», центральная часть свода имеет
блочную конструкцию. Нанесение огнеупорной массы на внутреннюю поверхность
свода позволяет минимизировать падение температуры;
-
свод
«печи-ковша, имеющий самонесущую конструкцию, с одной стороны поддерживается
вилочным порталом с направляющей стойкой, этим данная конструкция отличается от
обычных конструкций с двумя портальными кронштейнами;
-
в
центральной части свода находятся три отверстия для электродов;
-
свод
присоединен к системе пылеулавливания. Нижнее давление под сводом управляется
дополнительным компрессором и клапаном канала отходящих газов;
-
в
своде есть отверстия для фурмы измерения температуры и взятия проб, для подачи
легирующих, для аварийной фурмы, для подачи проволоки, а также измерения
давления в печи. Оба отверстия для продувки через фурму и для фурмы измерения
температуры и взятия проб закрываются шиберной заслонкой, приводимой в действие
пневматически.
3.
Портал
свода:
-
крышка
поднимается и опускается с помощью подъемной стойки свода, для того чтобы
находящийся под ним ковш мог выезжать и въезжать. Каждая установка «печь-кош»
имеет свой собственный портал;
-
подъемная
стойка свода оснащена косороликовой направляющей призматической формы. Цилиндр
подъема, приводимый в действие цилиндрически, интегрирован в подъемную стойку;
-
конечные
позиции свода контролируются конечным выключателем;
-
сводный
портал защищен предохранительным кожухом от излучения жидкой стали.
4.
Электродный
портал:
-
сдвоенная
установка «печь-ковш» оснащена только одним электродным порталом, обе установки
обслуживаются по очереди;
-
электродный
портал состоит из трех электродных подъемных стоек, а также каркаса с
поворотным устройством;
-
роликовые
опоры для направления опорных стоек встроены в портал установки на двух
уровнях. Подъемные стойки перемещаются на роликовых опорах. Следовательно,
ходовая поверхность подъемных стоек подвергается механической обработке,
поэтому ее необходимо содержать всегда в чистоте;
-
верхнее
и нижнее конечное положение подъемных стоек контролируются конечными
выключателями;
-
портал
гидравлически фиксируется в обоих конечных положениях (+60 и –60).
5.
Система
высокого тока. Электрическая энергия для процесса обработки на установке
«печь-ковш» подается от трансформатора по линии высокого тока на электроды. В
зоне подводящих шин высокого тока магнитные материалы подвергаются нагреванию
индукционным током, поэтому стена здания должна иметь как можно меньше металлического
армирования. Дальнейшая передача тока осуществляется через:
-
гибкие,
водоохлаждаемые кабели высокого тока;
- электропроводящие
электродные консоли;
-
зажимы
электрододержателя к графитным электродам, на конце которых образуются
электрические дуги.
6.
Стенд
свинчивания электродов. С точки зрения целесообразности, данный стенд размещен
в непосредственной близости от печи. Только таким образом можно избежать
простоев во время производственного процесса. Стенды свинчивания электродов
сконструированы таким образом, что снятые горячие электроды во время их
нахождения на стенде были защищены от тяги воздуха. Сам стенд состоит из рамы,
механического зажимного приспособления и защитной трубы. На нижнем конце
защитной трубы имеется смотровая дверца, которая делает возможным доступ к
острию электрода. Чтобы облегчить крановщикам посадку горячих электродов на
стенд и избежать насадки токопроводящей штанги электрода, стенд оснащается
воронкообразными отверстиями. Очень короткий электрод вводится в защитную трубу
до электродной коробки на нужной высоте и фиксируется механическим зажимным
приспособлением. Новая электродная частичная длина с ниппелем позиционируется с
помощью крана и специального подвеса с винтовым крючком. После того как
электродные коробки продуты сжатым воздухом и фронтальная поверхность очищена
от пыли, осуществляется ввинчивание новой частичной длины. Вблизи от стенда
свинчивания электродов предусмотрено место для складирования запаса электродов
на один день.
7.
Графитовые
электроды. Во время процесса обработки на установке «печь-ковш» электроэнергия
передается через графитовые электроды и с помощью электродуг – жидкому металлу.
Чтобы по возможности снизить потери активного сопротивления в электродах, они
должны обладать хорошей электропроводимостью. Кроме того, они должны
соответствовать следующим требованиям:
-
высокая
сопротивляемость по отношению к температурам внутри печи;
-
невосприимчивость
к смене температур;
-
достаточная
механическая прочность;
- хорошая устойчивость к
окислению кислородом воздуха.
Графитовые электроды
изготавливаются из особого сорта кокса (менее 1 % содержания золы). Этот сорт
кокса размельчается и обжигается во вращающейся трубчатой печи при температуре
1200ºС без доступа воздуха. В материал добавляют коксующиеся связки и
размешивают его до тех пор пока не образуется пластичная, готовая к прессовке в
теплом состоянии масса. В экструзионном процессе путем сильного сдавливания эта
смесь доводится до нужного диаметра. Возникающий таким образом “зеленый
электрод обжигается в кольцевой многокамерной печи в условиях отсутствия
доступа воздуха при температуре 1300ºС. После обжига электроды нагреваются
без доступа воздуха прямым прохождением тока до температуры 2600…3000ºС.
При этом кристаллы растут и в графите происходит кристаллическое упорядочивание.
Сразу после графитирования необожженные электроды чистятся и проверяются. Срок
изготовления графитовых электродов до их использования составляет от 8 до 12
недель. При особенно высоких нагрузках используются электроды качества LS или AGX, которые до
графитирования пропитываются пеком и дополнительно уплотняются отжигом.
8.
Продувка
инертным газом. Перемешивание металла для гомогенизации температуры и
химического состава осуществляется через два продувочных кирпича из огнеупорных
материалов, встроенных в днище ковша. Продувочные кирпичи окружены стальным
кожухом, который снабжается инертным газом. Инертный газ необходимо подавать
под давлением от 16 бар. Объем расхода инертного газа регулируется на
вентильном стенде и приспосабливается к различным этапам процесса обработки.
9.
Фурма
манипулятора (аварийная фурма). При повреждении донной продувки ковша можно с
помощью аварийной фурмы вдувать аргон в жидкий металл сверху. Аварийная фурма
состоит из стальной трубы, защищенной огнеупорным материалом. Фурма укрепляется
зажимным цилиндром, приводимым в действие гидравлически, на подъемно-опускаемом
механизме. При погружении фурмы в металл, шлак изнашивает огнеупорный материал,
поэтому фурму через определенный период времени использования необходимо
заменить. Для замены фурмы необходимо ослабить зажимный цилиндр и с помощью
крана поменять фурму. Аварийная фурма используется только в аварийных случаях,
так как ее использование и связанные с этим процессы обнаруживают значительно худшие
результаты, чем использование донной продувки.
10.
Манипулятор
для измерения температуры и взятия проб. Использование данного манипулятора
делает возможным измерение температуры стали, активности кислорода, зеркала
ванны и взятие пробы. Для этого фурму под наклоном (около 10 град.) погружают в
ванну на глубину приблизительно 500 мм. Измеренная глубина погружения
записывается (запоминается) и используется в этой плавке для других измерений,
происходящих на той же глубине жидкой стали.
11.
Циркуляционные
циклы охлаждающей воды. Охлаждающая вода необходима для частей, которые
особенно требовательны к температуре. К ним относятся: свод, консоли, кабели
высокого тока, трансформатор и др. На агрегате «печь-ковш» предусмотрены два
цикла циркуляции охлаждающей воды (табл. 4.1).
Таблица
4.1
Технические параметры
циркуляции охлаждающей воды
ЦИКЛ 1 |
|
Консоли |
3*50 м3/ч |
Кабель высокого тока |
3*7 м3/ч |
ЦИКЛ 1 |
|
Трансформатор |
60 м3/ч |
Температура воды,
первый слив/возврат |
350С / 450С |
ЦИКЛ 2 |
|
Крышка (свод) ковша |
2*230 м3/ч |
Температура воды,
первый слив/возврат |
350С / 500С |
6 КОНСТРУКЦИЯ И
ОБОРУДОВАНИЕ УСТАНОВКИ
ЦИРКУЛЯЦИОННОГО
ВАКУУМИРОВАНИЯ СТАЛИ
УЦВС состоит
из следующих основных узлов и агрегатов:
- несущие конструкции,
включая здания и фундаменты;
- вакуумная камера с двумя
патрубками;
- система подачи
нейтрального газа в патрубок вакуумной камеры для продувки и эрлифта металла;
- газоохладитель;
- вакуумпровод с шарнирным
соединением и вакуумным затвором;
- вакуумный пароэжекторный
насосный агрегат;
- механизм вертикального
перемещения вакуумкамеры;
- система хранения,
дозирования и загрузки ферросплавов в вакуумную камеру;
- пульт управления с ЭВМ
АСУ ТП, КИП и автоматикой;
- стенд разогрева и сушки
футеровки, ремонтные стенды;
- механизм для контроля
параметров жидкого металла (замер температуры, отбор проб);
- сталевоз для взвешивания
и транспортировки сталеразливочного ковша с металлом под вакуумкамеру.
1.
Вакуумная
камера представляет собой стальной резервуар, имеющий внутри три изоляционных
слоя и один слой огнеупорной футеровки, и состоящей из трех частей: днища,
корпуса и колпака. Камера имеет отверстия для добавки легирующих материалов,
для ввода нагревательного элемента и отвода отсасываемых газов. Нижняя часть
вакуумкамеры (днище) является съемным элементом и выполнена с двумя патрубками.
Конструкция
вакуумной камеры при этом обеспечивает:
- разогрев футеровки пред
обработкой плавки до температуры 1450…15000С и длительную эксплуатацию
устройства для разогрева в процессе вакуумной обработки;
- введение ферросплавов без
нарушения вакуума в процессе вакуумирования;
- удаление запыленных
газов;
- герметичность
подсоединения вакуумпровода, шлюзовой камеры, устройства для разогрева и др.;
- возможность наблюдения за
металлом и футеровкой в процессе вакуумирования;
- заполнение нейтральным
газом (азотом) вакуумкамеры по окончанию обработки;
- установку вакуумкамеры на
сталевоз и передачу ее на участок ремонта.
2.
Применяемый
на устанавливаемом агрегате вакуумирования пароэжекторный насос имеет ряд
неоспоримых преимуществ перед механическим вакуумным насосным агрегатом:
высокая производительность, отсутствие движущихся частей и нечувствительность к
пыли и влаге в газах. Вакуумный пароэжекторный насосный агрегат (ВПНА)
предназначен для создания разряжения в вакуумкамере и представляет собой
ступенчатую систему эжекторов со смесителями-конденсаторами и устройством для
создания предварительного разрежения. Пусковой блок агрегата состоит из одной
эжекторной ступени, после которой установлен конденсатор смешения.
Производительность пароэжекторного насоса может регулироваться путем выключения
его отдельных ступеней. Достигаемое конечное разряжение в вакуумкамере
составляет менее 0,5 мм.рт.ст. (50…70 Па). Управление насосом полностью
автоматизировано и осуществляется с пульта управления или ЭВМ АСУ ТП. При
установке пароэжекторного насоса предусмотрено также дожигание окиси углерода,
выбрасываемой в атмосферу в больших количествах при вакуумировании
нераскисленной стали. Для этой цели вся выбрасываемая из последней ступени
насоса паро-газовая смесь проходит через дополнительный конденсатор, где пар
конденсируется, а газ направляется на “свечу”, где, смешиваясь с воздухом,
сжигается. Одновременно предусмотрена вентиляция сливного бака и тракта водослива,
так как в них выделяется некоторое количество окиси углерода, выносимое водой
из конденсаторов в виде мелких пузырьков [27].
3.
Система
хранения, взвешивания и дозирования ферросплавов включает в себя:
- расходные бункера;
- весы - дозаторы;
- подвижный и стационарный
конвейер для подачи ферросплавов в металл;
- вибропитатели;
- вакуумный шлюз для
присадки ферросплавов в металл, предназначенный для приемки и подачи материалов
в вакуумкамеру в процессе обработки. Состоит из приемной воронки и шлюзовой
камеры.
4.
Газоохладитель
предназначен для охлаждения удаляемых из вакуумкамеры газов с целью уменьшения
их объема и предохранения шарнирных соединений вакуумпроводов от воздействия
высоких температур. Температура поступающих в газоохладитель газов – до 16000С,
выходящих из него – до 1000С. Газоохладитель представляет собой сварной
цилиндрический корпус с входными и выходными патрубками, внутри которого
размещен блок охлаждения. Блок охлаждения состоит из набора вертикальных
змеевиков, объединенных подводящим коллектором и отводящей полостью крышки. В
верхней части корпуса смонтирован клапан, который открывается при аварийном
повышении давления в системе. В нижней части корпуса имеется люк,
предназначенный для очистки газоохладителя от загрязнения, а также для сброса
воды при аварийных прорывах змеевиков.
5.
Вакуумпровод
шарнирный предназначен для герметичного подвижного соединения вакуумной
системы, смонтированной на площадке вакууматора, со стационарно установленным
вакуумным затвором. Вакуумпровод состоит из трубчатых колен, шарниров и опор
для них, а также из колец, вращающихся относительно друг друга на стандартных
телах качания с вакуумным уплотнением подвижных поверхностей манжетами. Одна
сторона шарнира стыкуется с неподвижным трубопроводом, а другая – с фланцем
одного из подвижных колен вакуумпровода. Неподвижное кольцо шарнира опирается
цапфами на подшипник опоры шарнирного вакуумпровода. Опоры шарнирного
вакуумпровода установлены на неподвижной площадке вакуумного затвора.
6.
Вакуумный
затвор предназначен для герметичного закрывания вакуумпроводов, а также для
дросселирования потока газа в процессе вакуумирования. Он представляет собой
герметичный сварной корпус, закрытый крышкой со встроенным в нее гидроцилиндром
и блоком клапанов. В горизонтальном входном патрубке встроена дроссельная
заслонка, поворачивающаяся вокруг горизонтальной оси и приводящаяся в движение
гидроцилиндром. Входной вертикальный патрубок вакуумного затвора присоединяется
к переходному трубопроводу перед пароэжекторным насосом.
7.
Система
электрообогрева вакуумкамеры предназначена для нагрева ее футеровки до рабочей
температуры (1450…15000С) и поддержания ее на этом уровне между циклами
вакуумирования. Нагрев производится графитовым электродом.
8.
Устройство
для замера температуры и отбора проб обеспечивает:
- автоматизированную
зарядку устройства пробоотборниками и термопарами;
- автоматизированный замер
температуры металла в ковше;
- автоматизированный отбор
проб металла из ковша;
- автоматизированную выдачу
проб в приемное устройство пневмопочты.
9.
Для
выполнения ремонтных работ и хранения сменных элементов вакуумкамеры комплекс
установки оборудован машиной обслуживания и специальными стендами.
6.1 Определение основных
размеров вакуумной камеры циркуляционного типа
Как показывает опыт
эксплуатации вакуумных установок циркуляционного типа, расход металла,
проходящего через вакуумную камеру, может быть определен из соотношения [28]:
Qм
= k*M/t,
где Qм - расход металла,
т/мин;
М – масса металла в
сталеразливочном ковше, т;
k - кратность циркуляции
(в зависимости от решаемых задач может колебаться в пределах 3…5);
t
- время, необходимое для вакуумирования металла, мин.
Размеры подъемного и
сливного патрубков приняты одинаковыми, следовательно площадь поперечного
сечения патрубков можно оценивать из условия максимальной мощности
перемешивания металла в ковше за счет истечения расплава из сливного патрубка.
Для определения мощности струи металла используем выражение:
W
= 500*S*r*u3,
где W – мощность струи, Вт;
S – площадь поперечного
сечения патрубка, м2;
r
- плотность металла, т/м3 (для жидкой стали - это 7,2 т/м3);
u – скорость истечения
металла, м/с.
Исследования, проведенные
сотрудниками МИСиС, позволили получить соотношение, связывающее между собой
поперечные сечения рукавов, скорость истечения металла, расход и уровень ввода
газа:
Qг
= S*(1,2*u+w)*u2/(m2*g*h-1,2*u2),
где Qг – расход несущего газа
при фактических значениях температуры и давления, м3/с;
g – ускорение силы
тяжести, м/с2;
h – уровень ввода несущего
газа, м;
m
- коэффициент расхода (для расчетов принимается m2 = 0,32);
w - скорость движения
газового пузыря относительно жидкости, м/с.
Величина w может быть оценена из
выражения:
w = 0,272*(s*g/r)1/4,
где s - поверхностное
натяжение на границе металл-шлак, Н/м.
Для металла можно принять
w
= 0,31 м/с.
Используя выражение для
мощности истекающей струи металла, можно получить:
W
= 500*r*Qг*(m2*g*h-1,2*u2)/u/(1,2*u+w)
Дифференцируя W по u и приравнивая
производную нулю, можно получить уравнение для определения оптимальной скорости
металла в сливном патрубке:
u3+1,25*w*u2-0,347*m2*g*h*w = 0.
Это уравнение может быть
решено численно, например, методом последовательных приближений.
При w = 0,31 м/с и m2 = 0,32 это уравнение
может быть записано в виде:
u3+0,39*u2 = 0,34*h = 0.
Это значит, что если
выбран уровень ввода газа h, то соответствующая ему скорость истечения металла в сливном
рукаве является оптимальной, то есть поддержание этой скорости в патрубке за
счет регулирования расхода газа, подводимого к подъемному рукаву, обеспечивает
максимальную скорость перемешивания в ковше.
Так как расход металла
через вакуумную камеру определен в зависимости от решения технологической
задачи коэффициентом кратности циркуляции, то площадь поперечного сечения
рукавов камеры может быть определена из соотношения:
S = Qм/(60*r*u) или S = k*M/(60*t*r*u).
По уравнению вычисляется
расход несущего Qг газа при фактических значениях температуры и давления. Остальные
параметры вакуумной камеры выбираются из конструктивных соображений.
В данном проекте
необходимо определить основные параметры вакуумной камеры циркуляционного типа
для обработки массы металла в ковше вместимостью 200 т и кратностью циркуляции k = 4. Время вакуумной
обработки t = 12 мин.
Скорость циркуляции
металла через вакуумную камеру:
Qм
= k*M/t = 4*200/12 = 66,7 т/мин.
Приняв уровень ввода
аргона в подъемный патрубок h = 1 м, получим скорость истечения металла в сливном
патрубке:
u3+
0,39*u3-0,34*h = 0
Отсюда: u = 0.63 м/с.
Площадь поперечного
сечения рукава и его диаметр:
S
= Qм/(60*r*u) = 66.7/(60*7,2*0,63) =
0,245 м2;
D
= 2*103*(S/p)1/2
= 2*103*(0.245/3.14)1/2 = 560 мм.
Расход несущего газа:
Qг = S*(1.2*u+w)*u2/(m2*g*h-1.2*u2) =
=0.245*(1.2*0.63+0.31)*0.632/(0.32*9.81*1-1.2*0.632) = 0.039 м3/с.
Для нахождения расхода
газа при нормальных условиях нужно определить уровень металла в вакууматоре.
Для этого необходимо определить поперечное сечение камеры. Диаметр камеры можно
найти из условия, что в днище должны разместиться два патрубка:
D1
>= 2*D+l1+2*l2,
где l1 – расстояние между
внутренними стенками патрубков, м;
l2 – расстояние от
внутренней стенки патрубка до цилиндрической части, м;
D – внутренний диаметр
патрубка, м;
D1 – диаметр вакуумкамеры,
м.
Расстояние между
патрубками l1
(рис. 6.1, 6.2) зависит от их конструкции и включает толщину внутренней футеровки
патрубков, толщину металлической арматуры патрубков и фланцев для их крапления,
если они разъемные, или толщину наружной футеровки:
l1
= 2*d1+2*d2+2*d3+d,
где d - расстояние между
кожухами патрубков для их возможного крепления (d = 300…400 мм);
d1
толщина рабочего слоя внутренней футеровки патрубка (периклазохромитовые
изделия толщиной 125 мм);
d2
толщина набивной массы между рабочим слоем и металлическим кожухом (d2
= 40 мм);
d3
толщина металлического кожуха (d3 = 20…30 мм).
Следовательно:
D1
>= 2*D+1.10,
м.
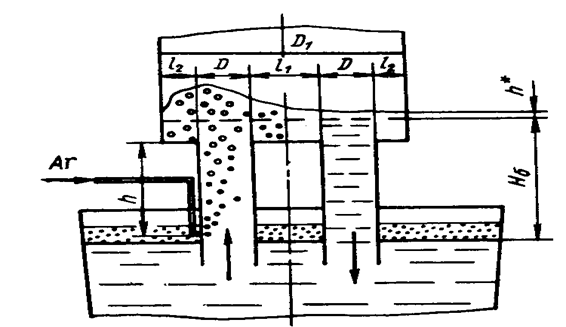
Рабочее пространство
циркуляционного вакууматора
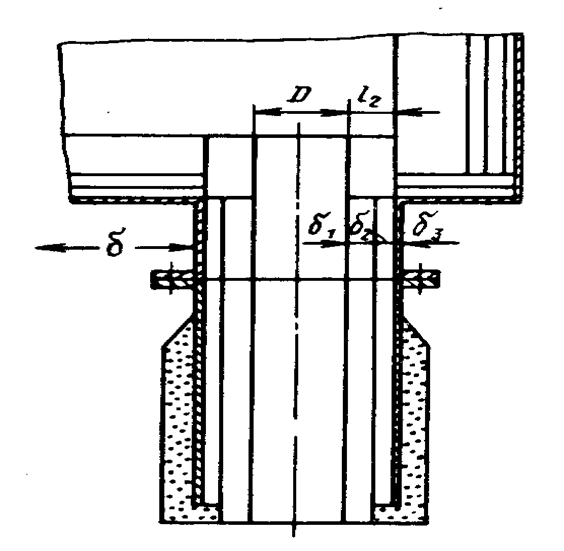
Футеровка патрубка
циркуляционного вакууматора
Принята конструкция
камеры со сменными патрубками при их диаметре D = 560 мм, тогда диаметр
камеры составит:
D1
= 2*D+1.10
= 2*0.56+1.10 = 2.22 м.
Площадь поперечного
сечения камеры при этом составит:
Sк
= p*(D1/2)2 = 3.14*(2.22/2)2 = 3.87 м2.
При скорости циркуляции
металла Qм
= 66,7 т/мин или 1,11 т/с, объем металла в камере составит:
Vм
= Qм/r
= 1.11/7.2 = 0.15 м3/с.
Увеличение уровня металла
при этом будет:
h* = Vм/Sк = 0,15/3,87 = 0,039 м.
Расход аргона при
нормальных условиях составит:
VAr = 6*104*Qг/n,
в свою очередь: n = 4,8*10-3*(T/h)*ln ( ),
где H – уровень металла в
камере после опускания ее в ковш с металлом (из опыта эксплуатации, этот
уровень может колебаться от 0 до 300 мм);
T – эффективная температура,
до которой нагревается аргон (обычно ~8000С).
При H = 100 мм расход газа
составит:
VAr = 6*104*0,039/8,08 =
289,6 л/мин.
7 ТЕХНОЛОГИЯ ОБРАБОТКИ
СТАЛИ
7.1 Сортамент
обрабатываемой стали
Внепечной обработке
подвергаются все марки стали, выплавляемые в цехе. Сортамент сталей,
выплавляемых на ККЦ №2, будет соответствовать сортаменту сталей, выплавляющихся
в пока еще действующем мартеновском цехе №1 ММК и предназначенных, в основном,
для получения сортовой заготовки. В данном проекте, на ККЦ №2 ММК предусмотрена
выплавка следующих марок стали:
1.
Углеродистая
сталь:
- кипящая обыкновенного
качества;
- кипящая качественная
конструкционная;
- полуспокойная
обыкновенного качества;
- полуспокойная
качественная конструкционная;
- спокойная обыкновенного
качества;
- спокойная качественная
конструкционная.
2.
Низколегированная
сталь (типа 35…38ХМ, 7ХНМ).
3.
Легированная
сталь (типа 25Х1МФ, 20ХГСНМ).
4.
Автоматная
сталь (типа А10).
В проектируемом цехе
предусмотрены следующие объемы производства по группам марок стали:
углеродистой – 85 %, низколегированной – 10 %, легированной – 4 % и автоматной
1 %.
7.2 Технология обработки
стали на установке «печь-ковш»
Установка
«печь-ковш» (АПК) предназначена для обработки жидкой стали в сталеразливочном
ковше, как с использованием установки циркуляционного вакуумирования стали
(УЦВС), так и без нее.
На АПК
осуществляются следующие технологические операции:
- продувка металла аргоном
для усреднения химического состава и его температуры по всему объему
сталеразливочного ковша;
- коррекция химического
состава металла;
- нагрев металла
электрической дугой;
- десульфурация металла
белым основным шлаком;
- измерение температуры и
отбор проб металла и шлака;
- микролегирование или
получение металла с узкими пределами содержания элементов путем ввода
порошковой проволоки с различными видами наполнителей.
Контроль над
процессом ковшевой обработки производится путем измерения температуры и
окисленности металла, отбора проб металла и шлака, измерения расхода и давления
аргона для продувки, измерения массы добавок, присаживаемых в ковш, измерения
тока и напряжения дуги и других электрических параметров, а также измерения
вспомогательных параметров (температура и давление охлаждающей воды, отходящих
газов и т.п.) [4].
В зависимости
от требований к химическому составу сталей и другим характеристикам, могут
использоваться следующие схемы внепечной обработки сталей [24]:
1.
Конвертер
АПК – МНЛЗ.
2.
Конвертер
УЦВС – АПК – МНЛЗ.
3.
Конвертер
АПК – УЦВС – МНЛЗ.
Ферросплавы,
используемые на установке «печь-ковш», должны иметь фракцию от 5 до 50 мм,
соответствовать требованиям государственных стандартов и технических условий.
Влажность не должна быть более 1 %.
Кокс кусковый
должен иметь фракцию до 25 мм по СТП 14-101-206-98.
Алюминий для
раскисления, легирования и коррекции химического состава стали должен отвечать
ТУ 48-0102-49-91, ГОСТ 11070-74 и ГОСТ 295-79 соответственно.
Применяемая
известь должна быть только свежеобожженной по СТП ММК 223-99.
Плавиковый
шпат должен иметь влажность не более 1 % и соответствовать ГОСТ 29220-91.
Подаваемый
аргон должен иметь массовую долю аргона не менее 99,5 % и отвечать требованиям
ГОСТ 10157-79. Давление аргона в сети – не менее 10 кг/см2 (1 МПа).
Азот газообразный
должен соответствовать ГОСТ 9293-74.
Применяемые
пробоотборники должны соответствовать ТУ 311-00226253.046-94.
Термопары
ТУ 311-0226258.017.
Применяются
датчики окисленности жидкого металла типа «Celox»
Перед
обработкой металла на установке необходимо обеспечить:
- заполнение бункеров
необходимыми материалами, соответствующим требованиям ГОСТов;
- наличие средств отбора
проб металла, измерения температуры и окисленности;
- подачу газов необходимого
давления;
- подачу воды на охлаждение
элементов установки до требуемых параметров;
- исправность работы систем
продувки металла аргоном;
- исправность работы
газоотводящего тракта;
- исправность работы всех
механизмов, систем контроля, управления, сигнализации и блокировок;
- исправность работы пневмопочты;
- проверку длины электродов
и по необходимости их наращивание.
Технология
обработки металла на АПК по схеме «Конвертер – АПК – МНЛЗ», сводится к
следующему:
- плавка, предназначенная
для обработки на АПК, сливается в сталеразливочный ковш, специально
оборудованный для донной продувки. Ковш должен иметь исправную сухую футеровку.
Верхний край ковша должен быть чистым;
- раскисление, легирование
и обработка металла твердыми шлакообразующими смесями во время выпуска плавки
из конвертера производится согласно имеющейся в цехе технологической
инструкции. Легирующие присаживаются из расчета получения содержания Si, Mn, Al на нижнем пределе;
- производится качественная
отсечка конвертерного шлака во время выпуска металла в сталеразливочный ковш;
- уровень налива металла в
ковше должен быть 400…1000 мм от верхней кромки ковша (величина уровня налива
может уточняться в процессе освоения технологии);
- поступивший из
конвертерного отделения сталеразливочный ковш устанавливается на сталевоз
агрегата «печь-ковш». К продувочным устройствам подсоединяются аргонные шланги,
включается подача аргона с расходом 15…30 м3/ч на каждое из продувочных
устройств (расход аргона может уточняться в процессе освоения технологии);
- сталевоз передвигается
под крышку АПК, после чего крышка опускается. Через рабочее окно производится
корректировка интенсивности продувки. Расходы аргона должны обеспечивать
минимальное оголение поверхности металла;
- через 1…2 минуты продувки
производится измерение температуры и окисленности метала. На основании
показаний содержания кислорода в металле вводится расчетное количество
алюминиевой катанки для предварительного раскисления металла. Ориентировочный
расход алюминия приведен в табл. 7.1.;
- при проведении процесса
десульфурации металла в ковше должен быть наведен белый высокоосновный
жидкоподвижный шлак. Для этого в ковш присаживается известь и плавиковый шпат в
соотношении 4:1. Расход шлакообразующих материалов может составлять до 10 кг/т
(расход уточняется в процессе освоения технологии). Материалы вводятся порциями
не более 150 кг;
- для нагрева металла и
расплавления шлака электродный портал поворачивается в исходную позицию и
производится включение установки на 5 минут на средней ступени нагрева;
- после расплавления жидкий
шлак раскисляется присадкой алюминия в количестве 50…100 кг (уточняется
исследованиями);
- после окончания процесса
нагрева, через 3 минуты перемешивания металла аргоном, производится измерение
температуры металла и отбираются пробы металла и шлака и отправляются в
экспресс-лабораторию. Проба шлака берется с помощью металлической
трубки-стержня через рабочую дверцу, далее она охлаждается и анализируется
визуально по цвету и поверхности. Цвет шлака меняется по степени его
окисленности (содержания FeO) от черного к белому. Появление белого шлака в
ковше означает, что шлак нормально подготовлен для проведения процесса
десульфурации стали. При отклонении цвета и поверхности шлака от рекомендуемых,
необходимо принять меры по исправлению химического состава шлака. Ориентировочный
визуальный анализ состава шлака и способы его исправления представлены в табл.
7.2. Для обеспечения наилучшего результата десульфурации стали в ковше,
содержание в шлаке (FeO)+(MnO) должно быть менее 1,5 %. Оптимальный состав ковшевых шлаков для
проведения десульфурации представлен в табл. 7.3.;
- после получения
результатов химического анализа металла производится корректировка его
химического состава добавлением необходимого количество ракислителей и
легирующих материалов из расчета получения среднего содержания элементов. Затем
металл перемешивается аргоном не менее 5 минут. Для интенсификации растворения
ферросплавов расход аргона разрешается увеличить до 30…40 м3/ч (уточняется в
процессе исследований);
- не ранее чем через 5
минут продувки, после присадки ферросплавов измерить температуру металла и
отобрать пробы металла и шлака. До получения результатов экспресс-анализа
производить перемешивание металла аргоном с расходом 10…20 м3/ч (уточняется
исследованиями);
- при получении результатов
химического анализа в случае необходимости произвести дополнительную
корректировку химического состава металла;
- легкоокисляющиеся
элементы вводятся в ковш только после окончания последнего цикла нагрева. В
стали, с оговоренным содержанием кальция, вводят трайб-аппаратом порошковую SiCa или AlCa проволоку без продувки
аргоном для достижения максимально высокого усвоения элементов. Если
наблюдается белое пламя над шлаком, то необходимо увеличить скорость ввода
порошковой проволоки;
- если температура металла
ниже указанной для МНЛЗ, то необходимо произвести дополнительный нагрев;
- при необходимости
охлаждения металла, охлаждение производить слябом;
- через 3 минуты после
окончания последнего цикла нагрева произвести замер температуры и отбор пробы металла.
После достижения необходимого химического состава и заданной температуры
электродный портал поворачивается в другую сторону. Крышка АПК поднимается,
сталевоз с ковшом выдвигается из-под агрегата, отсоединяется аргонный шланг и
далее ковш передается на МНЛЗ.
Обработка стали по схеме
«Конвертер – УЦВС – АПК – МНЛЗ»:
- перед подачей плавки на
агрегат «печь-ковш» металл подвергается обработке на установке циркуляционного
вакуумирования стали в соответствии с имеющейся в цехе инструкцией по
внепечному вакуумированию жидкой стали;
- после окончания вакуумной
обработки ковш передают на АПК и проводят внепечную обработку в соответствии с
вышеизложенной схемой;
- при обработке сталей с
низким и особонизким содержанием углерода следует учитывать возможное науглероживание
металла от электродов.
Обработка
стали по схеме «Конвертер – АПК – УЦВС – МНЛЗ» производится при необходимости
вакуумной обработки металла с целью дегазации. При этом обработка плавки на АПК
производится согласно вышеописанной, первой схеме обработки металла, затем
металл обрабатывается на УЦВС в соответствии с технологической инструкцией по
вакуумированию стали в цехе.
При невозможности
продувки металла аргоном через донные фурмы, необходимо:
- проверить все соединения
трубопроводов, по которым подается аргон. При наличии утечек аргона их
устранить;
- дать максимальный расход
аргона через 'байпас'. Если 'раздутия' пробки не произошло, то необходимо
продувку аргоном производить аварийной верхней фурмой;
- по окончании
усреднительной продувки, поднять фурму и произвести замер температуры и
окисленности, также отобрать пробы металла и шлака. Пробы направляются в
экспресс-лабораторию (проба шлака оценивается визуально);
- после отбора проб и
замере температуры, по необходимости осуществляется ввод шлакообразующих
материалов, затем опускаются электроды, и в течение 4…6 мин производится нагрев
металла. Одновременно с нагревом производится продувка металла аргоном через
аварийную фурму с максимальным ее заглублением. Расход аргона должен обеспечивать
минимальное волнение поверхности металла;
- затем производится
измерение температуры и отбор проб металла и шлака;
- после получения
результатов экспресс-анализа в металл вводится в необходимом количестве
ферросплавы;
-
окончание
обработки производится по описанной выше технологии.
Таблица 7.1
Ориентировочный
расход алюминия для раскисления металла
Содержание кислорода в металле, ppm |
100 |
200 |
300 |
400 |
500 |
600 |
700 |
800 |
900 |
1000 |
Расход алюминия, кг |
40 |
80 |
120 |
160 |
200 |
240 |
280 |
320 |
360 |
400 |
Таблица 7.2
Визуальный анализ состава ковшевого шлака
По цвету
|
Черный
|
Содержание (FeO+MnO)>2%. Шлак необходимо дополнительно
раскислить Al или Si. |
Серый |
Содержание (FeO+MnO)=1…2 %. Необходимо дальнейшее
раскисление шлака Al или Si. |
Белый – желтый |
Шлак нормально раскислен. Желтый цвет указывает, что
десульфурация прошла. |
По цвету
|
Зеленый |
Шлак содержит оксид хрома (Сr2O3). |
По поверхности
|
Зеркальная – гладкая,
тонкая
|
Высокая доля (SiO2, Al2O3). Необходима добавка извести порциями по 0,4 кг/т. |
Гладкая и толстая |
В холодном состоянии шлак должен распадаться. Если он не
распадается, то высокая доля (Al2O3). Необходима добавка порций извести по
0,4 кг/т. |
Шероховатая, неровная |
Высокая доля (CaO). Если
имеются нерастворенные частицы извести, то необходима добавка песка (SiO2) или глинозема (Al2O3) порциями не более 0,1 кг/т. |
Таблица 7.3
Оптимальный химический состав ковшевых
шлаков для десульфурациии стали
Компонент
|
Содержание в шлаке, %
|
Сталь, раскисленная кремнием |
Сталь, раскисленная алюминием |
CaO |
55…65 |
55…65 |
SiO2 |
20…30 |
5…10 |
Al2O3 |
5…10 |
20…30 |
MgO |
4…5 |
4…5 |
FeO+MnO |
1 |
0.5 |
7.3 Технология обработки
стали на установке
вакуумирования
циркуляционного типа
Процесс
циркуляционного вакуумирования заключается в обработке вакуумом металла,
непрерывно текущего через вакуумкамеру по двум патрубкам, опущенным в
сталеразливочный ковш с расплавом. Для обеспечения непрерывного подъема металла
в камеру в один из патрубков подается аргон, пузырьки которого в результате
большой разницы плотностей , поднимаясь вверх по патрубку, увлекают за собой
расплав выполняя функции транспортирующего газа. В камере металл дегазируется
и, становясь более плотным и тяжелым, сливается по второму патрубку в ковш.
Во время
прохождения жидкого метала через вакуумкамеру под действием разрежения,
создаваемого пароэжекторным насосом, происходят процессы удаления из стали
растворенных газов (кислорода, водорода, частично азота), углеродное
раскисление или обезуглероживание стали. Выделяющиеся в вакуум пузыри моноокиси
углерода и инертного газа (аргона), приводят к интенсивному диспергированию
металла и интенсификации процессов дегазации и перемешиванию стали в
вакуумкамере. Вследствие повышения раскислительной способности углерода при
низких парциальных давлениях моноокиси углерода, значительная часть кислорода (до
60 %) удаляется из стали в виде СО, что повышает чистоту металла по содержанию
в нем неметаллических включений и уменьшает угар элементов-раскислителей,
вводимых в сталь. Снижение активности кислорода в металле при вакуумировании,
наряду с интенсивным перемешиванием жидкой стали в вакуумкамере, способствует
лучшему усвоению присаживаемых добавок [27].
С целью
увеличения срока службы вакуумной камеры и патрубков, в начале обработки и за 1
минуту до окончания вакуумирования на поверхность металла в вакууматоре через
вакуумный шлюз подают порцию нейтрализатора шлака в количестве 50…100 кг. В
качестве нейтрализатора шлака применяют брикеты на основе глинозема (Al2O3).
Для снижения
тепловых потерь металла при вакуумировании и улучшения условий службы огнеупоров,
футеровка вакуумкамеры постоянно поддерживается в разогретом состоянии
(1450…15000С) за счет теплоизлучения графитового нагревателя, являющегося
резисторным элементом электрической системы разогрева вакуумкамеры. С целью
уменьшения эрозии футеровки вакуумкамеры и патрубков, в периоды между
обработками плавок на УЦВС, объем вакуумкамеры заполняется азотом, а патрубки
погружаются в песок.
Ферросплавы,
используемые на установке циркуляционного вакуумирования стали, должны иметь
фракцию от 5 до 50 мм и соответствовать требованиям государственных стандартов
и технических условий. Влажность не должна превышать 1 %.
Применяемый
на установке нейтрализатор шлака должен отвечать требованиям СТП-101-73-89.
Газообразный
аргон, с массовой долей аргона не менее 99,5 % должен соответствовать
требованиям ГОСТ 10157-79. Азот – ГОСТ 9293-74. Давление газов в сети должно
быть не менее 0,8 МПа.
К началу
вакуумной обработки стали установка должна быть полностью подготовлена к
работе. Это означает:
А. Все
механизмы, органы управления и футеровка вакуумкамеры находятся в исправном
состоянии.
Б. Установка
обеспечена всеми необходимыми энергоресурсами требуемых параметров:
- аргон и азот: давление
0,8…1,0 МПа;
- вода технически очищенная
на пароэжекторный насос: давление 0,1…0,4 МПа с температурой не более 35 0С;
- вода химически очищенная
на механизм электронагрева: давление 0,5 МПа;
- сжатый воздух: давление
0,7 МПа;
- пар: давление 1,3 МПа и
температура 200 ± 50 0С;
- электроэнергия: рабочее напряжение
36…360 В;
- вода технически очищенная
на газоохладитель и уплотнения: давление 0,5 МПа.
В. Все
системы сигнализации и АСУ ТП «Вакуумирование» исправны.
Г. Футеровка
вакуумкамеры нагрета до температуры не менее 14500С (измеряется термодатчиками
и отображается на дисплеях АСУ ТП).
Сталеразливочный
ковш, подаваемый под плавку для вакуумирования, должен иметь исправную сухую
футеровку без мусора и настылей. Толщина шлака в ковше должна быть не более 100
мм, а уровень наполнения ковша металлом и шлаком – на 100…150 мм ниже верхней
кромки ковша.
Цикл
вакуумной обработки начинается с установки шлакоотделителей на патрубки
вакуумной камеры. При погружении вакуумной камеры в металл, в ней создают
избыточное кратковременное давление азота для вытеснения попавшего в патрубки
шлака. Погружение патрубков производят до глубины, предотвращающей подсосы
воздуха и ковшевого шлака в камеру. Затем включается вакуумный насосный
агрегат, и металл вследствие разности давлений между камерой и атмосферой
поднимается по обоим патрубкам в камеру на барометрическую высоту (около 1,4
м). Одновременно в нижнюю часть всасывающего патрубка подается аргон, который,
поднимаясь вверх и увеличиваясь в объеме, образует газо-металлическую эмульсию
с соотношением газа к металлу 10:1. Со скоростью более 5 м/с такая эмульсия
врывается в камеру, образуя высокий бурун над всасывающим патрубком. Наличие
большого количества транспортирующего газа способствует созданию огромной
дополнительной реакционной поверхности, интенсифицируя процесс дегазации
металла. Этим объясняется то обстоятельство, что, несмотря на сравнительно
небольшое время пребывания расплава в камере, обычно не превышающее нескольких
секунд, металл поступает в сливной патрубок практически полностью
дегазированным. Из сливного патрубка этот металл, попадая снова в ковш,
смешивается с находящимся в нем расплавом, несколько разбавляя в нем содержание
газов. Поэтому для более глубокой дегазации весь металл ковша необходимо
пропустить через камеру не менее 2,5…5 раз в зависимости от степени раскисления
[25].
В зависимости
от назначения металлопродукции, а также технологических целей использования
вакуумной установки, различают следующие виды обработки стали:
- глубокое удаление
водорода, вакуумное углеродное раскисление, рафинирование от неметаллических
включений, доводка по химическому составу и температуре, окончательное
раскисление и легирование алюминием;
- доводка по химическому
составу и температуре, окончательное раскисление алюминием и удаление водорода;
- глубокое обезуглероживание
стали в вакууме, дегазация, доводка по химическому составу и температуре,
раскисление;
- усреднение и коррекция
химического состава и температуры, а также окончательное раскисление.
Вакуумированию
подвергаются плавки как непосредственно после выпуска из конвертера, так и
после обработки на агрегате «печь-ковш». Для проведения всех технологических
операций при вакуумировании стали типа 08Ю, выпуск из конвертера должен
производиться не менее, чем за 60 минут до начала разливки на МНЛЗ, а для
трансформаторной стали – не менее 80 минут.
Перед началом
обработки измеряют температуру металла, толщину слоя шлака в ковше и отбирают
пробу для определения химического состава стали. Температура металла измеряется
термопарой погружения и отображается на измерительном приборе. Температура
металла в ковше перед вакуумированием должна быть на 40…50 0С выше температуры
разливки, но не более 1630 0С. При температуре металла выше требуемой до начала
вакуумирования производится охлаждение металла слябом.
По данным
измерений и результатам химического анализа пробы стали, отобранной перед
вакуумированием, учитывая массу плавки и заказанную марку стали, оператор
выбирает программу обработки и режим управления. Процесс вакуумирования может
производиться в автоматическом или ручном режиме. В первом случае оператор
вводит программу в ЭВМ АСУ ТП «Вакуумирование» и по команде оператора
вакууматор включается в работу по заданной программе. Вакуумирование в ручном
режиме осуществляет оператор с пульта управления, при этом он имеет возможность
воспользоваться режимом «совет мастера».
Вакуумное
обезуглероживание низкоуглеродистой нераскисленной стали производится до
минимально возможного снижения остаточного давления в вакуумной камере (менее 1
мм.рт.ст.) и до достижения кратности циркуляции не менее трех. Известно также,
что обработка металла при давлении более 0,53 кПа (4 мм.рт.ст.) не обеспечивает
требуемую дегазацию стали.
Длительность
вакуумирования определяется совокупностью осуществляемых технологических
операций и регламентируется скоростью циркуляции, которая зависит от расхода
аргона и внутреннего диаметра патрубков.
Масса,
марочный сортамент и очередность присаживаемых ферросплавов и раскислителей в
вакуумную камеру определяется маркой стали и технологией вакуумной обработки.
Корректирующие присадки среднеуглеродистого (до 2 % углерода) и
высокоуглеродистого (до 7 % углерода) ферромарганца при обработке
особонизкоуглеродистых марок стали производятся в период вакуумного
обезуглероживания.
Присадки
материалов в вакуумкамеру осуществляются со скоростью не более 2 т/мин. При
этом масса одной порции не должна превышать : ферромарганец – 350 кг;
ферросилиций – 250 кг; силикомарганец – 350 кг; ферованадий – 250 кг;
ферротитан – 250 кг; алюминий – 250 кг; нейтрализатор шлака – 100 кг; руда,
окатыши, агломерат – 50 кг; углеродосодержащий материал – 50 кг; скрап, сечка
350 кг [21].
При расчете
количества присадок на плавку в процессе вакуумной обработки руководствуются
следующими ориентировочными величинами усвоения элементов: марганец – 90…95 %;
кремний – 85…90 %; алюминий – 30…60 %; титан – 50…70 %; углерод – 40…50 %;
ванадий – 80…90 %; ниобий – 80…90 % [26].
После
введения добавок для корректировки химического состава стали и раскисления
производится перемешивание металла с кратностью циркуляции не менее 0,5 в
течение 3…5 минут. Расход аргона в подъемный патрубок при этом максимальный.
После
окончания процесса вакуумирования, закрывают главный вакуумный затвор,
выключают вакуумный насос, включают систему заполнения вакуумкамеры азотом. При
достижении атмосферного давления, вакуумкамера поднимается из сталеразливочного
ковша. Система подачи аргона в патрубок переключается на азот с минимальным
расходом, отбирается проба стали и замеряется температура металла. При
получении необходимого химического состава и заданной температуры металла ковш
передается на МНЛЗ [25].
При лимите
времени на вакуумную обработку, возможна корректировка химического состава
стали и усреднение металла по температуре на агрегате «печь-ковш».
8 АВТОМАТИЗАЦИЯ ПРОИЗВОДСТВЕННЫХ
ПРОЦЕССОВ
Развитие
современного металлургического производства сопровождается интенсификацией
технологических и производственных процессов. Создание крупных металлургических
агрегатов и их комплексов позволяет более эффективно использовать сырье,
топливо, капиталовложения. В то же время осуществлять управление
интенсифицированными металлургическими процессами в больших и сложных
технологических объектах без использования новейших методов и средств
управления – неэффективно или вообще невозможно.
Наиболее
эффективным средством управления технологическими объектами являются системы
централизованного управления, создаваемые на основе теории управления,
использующие экономико-математические методы, вычислительную и управляющую
технику. Такие системы управления получили наименование автоматизированных
систем управления технологическими процессами (АСУ ТП).
Для
достижения высоких качественных и технико-экономических показателей работы как
конвертерного цеха в целом, так и отделения ковшевой обработки стали в
частности, предусматривается их оснащение автоматизированными системами
управления технологическим процессом, которые обеспечивают:
- достижение максимальной
производительности за счет рационального управления технологическими
процессами;
- повышение качества стали
за счет обеспечения операторов информацией о ходе процессов, а также
своевременной выдачи рекомендаций и управляющих воздействий;
- повышение выхода годного
металла;
- снижение простоев
оборудования;
- снижение сырьевых и
энергетических затрат на производство стали;
- улучшение условий труда
производственного персонала.
АСУ включает
подсистемы, реализующие управляющие, информационные и расчетные функции в
соответствии с функциональной структурой.
В состав
интегрированной АСУ входят следующие взаимосвязанные автоматизированные системы
управления [6]:
- АСУ процессом
производства стали в кислородно-конвертерном цехе (АСУ «Производство»);
- АСУ технологическим
процессом подготовки шихтовых материалов и выплавки стали в конвертере (АСУ ТП
«Плавка»);
- АСУ процессом внепечной
обработки стали на агрегате «печь-ковш» (АСУ ТП «Доводка»);
- АСУ процессом
вакуумирования стали (АСУ ТП «Вакуумирование»);
- АСУ процессом разливки
стали на МНЛЗ (АСУ ТП «Разливка»).
В отделении
ковшевой обработки стали применяются АСУ ТП «Доводка» и АСУ ТП
«Вакуумирование».
С целью
обеспечения нормальной эксплуатации систем автоматики, управления и
электрооборудования предусмотрены специальные поверочные устройства.
8.1 Общецеховая АСУ
«Производство»
АСУ «Производство»
является элементом интегрированной АСУ ККЦ и предназначена для планирования,
управления, учета хода производства, технико-экономического анализа, а также
обеспечения информацией смежных систем верхнего и нижнего уровней.
АСУ
«Производство» включает в себя четыре подсистемы:
- подсистему оперативного
планирования производства;
- подсистему
информационного обеспечения производства;
- подсистему учета
технико-экономического анализа хода производства;
- исследовательскую
подсистему.
1.
В
подсистему оперативного планирования входят:
- оперативное планирование,
обеспечивающее формирование и оперативную корректировку компактного графика;
- расчет потребности в
основном сырье;
- анализ обеспечения МНЛЗ
металлом с учетом месячной спецификации для выполнения заказов.
Оперативное
управление выполнения контактного графика включает:
- направление плавки на
технологическую операцию;
- выдачу задания на
подготовку ферросплавов;
- слежение за потребностью
в чугуне, в совках с металлоломом, в сыпучих шихтовых материалах и
ферросплавах;
- слежение за выполнением
сменно-суточного задания;
- анализ необходимости
пересчета контактного графика.
2.
Подсистема
информационного обеспечения персонала, выполняет следующие функции:
а) ответы на
запросы персонала с выдачей данных:
- о количестве и
характеристиках шихтовых материалов;
- о ходе выплавки стали в
конвертере;
- о химическом составе
чугуна, стали и шлака;
- о длительности периодов
выплавки и обработки стали;
- о межплавочных простоях;
- о виде и ходе внепечной
обработки плавки.
б)
формирование плавильного журнала и итоговых данных за смену;
в) информация
о состоянии агрегатов и оборудования;
г) информация
о наличии шихтовых материалов.
3.
Подсистема
учета и технико-экономического анализа хода производства реализует такие
функции:
а) учет
производства, включающий:
- производство металла;
- расчет плана производства
за сутки и с начала месяца;
- выполнение плана
производства.
б) учет
использования рабочего времени;
в) учет
расхода шихтовых материалов;
г) контроль
за качеством металла;
д) учет
стойкости оборудования, включающий продолжительность межремонтного периода основного
оборудования;
е) расчет
технико-экономических показателей.
8.2 АСУ ТП «Доводка»
Основные
функции АСУ ТП «Доводка» следующие:
1.
Информационные:
- измерение химического
состава и массы жидкого металла в ковше;
- измерение температуры и
окисленности металла в ковше;
- расход порошковых
материалов, вдуваемых в ковш;
- расход аргона на
транспортировку материалов, вдуваемых в ковш;
- давление и расход аргона
на продувку металла в ковше;
- количество и температура
отходящих газов в ковше, их состав;
- давление под
уплотнительной крышкой ковша;
- содержание кислорода под
уплотнительной крышкой ковша;
- электрические параметры нагрева
металла в ковше;
- положение графитовых
электродов;
- масса алюминиевой и
порошковой проволоки, вводимой в ковш;
- продолжительность
электродугового нагрева, продувки аргоном, вдувания порошков и суммарное время
обработки.
2.
Управляющие:
- управление взвешиванием,
транспортировкой и подачей порошкообразных материалов;
- управление взвешиванием,
транспортировкой и подачей ферросплавов, легирующих и модифицирующих кусковых
материалов;
- расчет и подача
количества алюминия;
- управление электродуговым
нагревом металла;
- управление газоотводящим
трактом;
- управление продувкой
металла аргоном;
- регистрация отклонений
контролируемых параметров от заданных значений и др.
Режимы работы
АСУ ТП «Доводка»:
- ручной, наладочный;
- дистанционный (с поста
управления);
- «совет мастеру», когда
система дает рекомендации по ведению процесса;
- автоматизированный, при
котором работа оборудования происходит по командам вычислительного комплекса.
8.3 АСУ ТП
«Вакуумирование»
АСУ ТП
«Вакуумирование» выполняет следующие основные функции:
1.
Информационные:
- масса стали в ковше;
- масса стали в
вакууматоре;
- температура металла в
ковше;
- уровень металла и шлака в
ковше;
- окисленность металла в
ковше;
- содержание углерода в
стали по температуре ликвидус;
- температура стенок,
футеровки и рабочего пространства а период нагрева вакуумкамеры;
- остаточное давление
(вакуум) в вакуумкамере;
- температура газов после
охладителя;
- расход., давление и
количество подаваемого аргона;
- расход, давление и
количество азота;
- расход, давление и
количество воды на газоохладитель, на охлаждение электрододержателя;
- уровень воды в
газоохладителе;
- уровень материалов в
бункерах ферросплавов и ы шлюзовом устройстве;
- параметры энергоносителей
к пароэжекторному насосу;
- расход, давление
природного газа и воздуха на сушку вакуумкамеры.
Сбор и
обработка информации построена на базе микропроцессорных контроллеров
«Димиконт» и «Ломиконт», а также вычислительного комплекса СМ-1800 [6].
Функции
регулирования давления аргона и азота и управления их подачей, а также
регулирования расхода природного газа и соотношения газ-воздух, подаваемых для
сушки футеровки вакуумкамеры на стенде, выполняет логический микропроцессорный
контроллер («Ломиконт»).
Для
возможности дистанционного управления регулирующими клапанами предусмотрены
блоки управления БРУ и задатчики РЗД.
Кроме того,
«Ломиконт» выполняет функции управления пароэжекторным насосом и дожигающим
устройством.
Для
отображения информации применен дисплейный микропроцессорный контроллер
(«Домиконт», который по команде оператора или программно формирует и
высвечивает на экране дисплея мнемосхемы, таблицы, графики, гистограммы, а
также осуществляет допусковый контроль технологических параметров и параметров
оборудования, сигнализацию отклонения параметров от заданных значений и печать
протокола процесса вакуумирования.
Вычислительным
комплексом СМ-1800 производится:
- расчет массы металла в
вакууматоре;
- расчет массы присадок и
управления их подачей;
- прогнозирование состава и
температуры металла по ходу процесса вакуумирования;
- обмен информацией с
цеховой АСУ «Производство»;
- контроль работы горелок
стенда сушки и устройства дожигания отходящих газов;
- контроль факела
дожигающего устройства;
- давление газа к горелкам
дожигающего устройства;
- сигнализация отклонения
параметров вакуумирования от заданных.
2.
Управляющие:
- движением вакуумкамеры;
- расчет массы присадок и
управление их подачей;
- пароэжекторным насосом;
- дожигающим устройством;
- подачей и стабилизации
давления аргона и азота, подаваемых в вакуумкамеру.
Объем
автоматического контроля и регулирования представлен на схемах автоматизации
(рис. 8.1, 8.2).
8.4 Связь
Проектом
предусмотрены следующие виды связи:
- связь с помощью телефонов,
включенных в цеховую АТС;
- диспетчерская телефонная
связь абонентов цеха с цеховым диспетчером, спомощью коммутаторов;
- прямая двухсторонняя
громкоговорящая связь с помощью аппаратуры ПТС-А «Прогресс»;
- распорядительно-поисковая
громкоговорящая связь;
- административная связь
руководителей цеха с подчиненными с помощью коммутаторов;
- технологическое и
диспетчерское промышленное телевидение;
- радиосвязь машинистов
кранов с операторами.
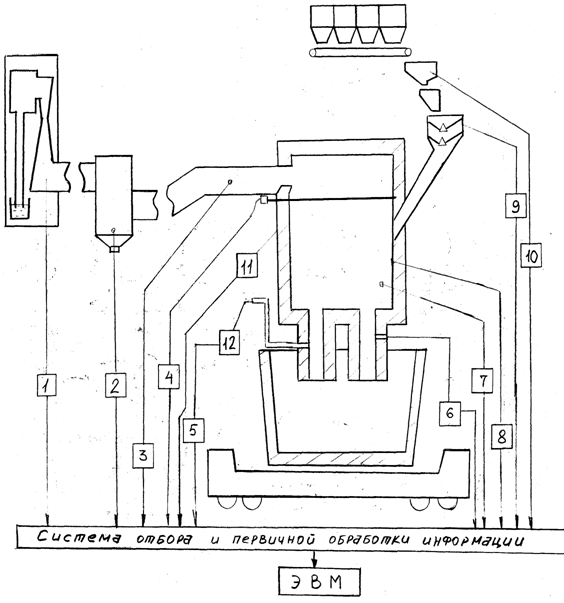
Схема автоматизации
вакууматора
1 – контроль работы
вакуумного пароэжекторного насоса; 2 – измерение температуры отходящих газов; 3
определение состава отходящих газов; 4 – контроль работы графитового
электрода для нагрева вакуумкамеры; 5 – контроль расхода подаваемого аргона; 6
определение химического состава и температуры обрабатываемого металла; 7
измерение остаточного давления в вакуумкамере; 8 - измерение температуры
футеровки вакуумкамеры; 9 – контроль системы загрузки сыпучих и ферросплавов;
10 – определение массы подаваемых сыпучих и ферросплавов; 11 – контроль
положения вакуумкамеры; 12 – контроль давления подаваемого аргона и определение
объема аргона за весь цикл обработки
Приложение 1
Выбор и
расчет количества основного технологического
оборудования отделения
ковшевой обработки стали
1
Технологическое
оборудование
1.1.
Сталеразливочные
ковши
Вместимость
сталеразливочного ковша определяется вместимостью конвертера, и в проектируемом
цехе составляет 220 т при вместимости конвертера 200 т [*].
Число
сталеразливочных ковшей в цехе (Nск) рассчитывается по формуле:
Nск
= *(tз + ) + nрм + nз ,
где n - число ковшей стали, разливаемых
за сутки, шт;
tз
задолженность сталеразливочного ковша на разливке одной плавки (составляет
6,5 ч) [*];
tрф
затраты времени на ремонт футеровки ковша (составляют 15,6 ч);
nрм и nз – соответсвенно число
ковшей на капитальном ремонте (кожуха, механических устройств и пр.) и запасных
(обычно по одному), шт;
Ф – стойкость
футеровки ковша (составляет 10…15 плавок);
С
коэффициент, учитывающий организационные задержки (принимается равным 0,8).
Число ковшей
стали, разливаемых за сутки, соответствует числу плавок:
n = ,
где N - число постоянно
работающих конвертеров, шт;
t - длительность
цикла конвертерной плавки (см. п.2.1.), мин.
Принимаю:
- стойкость монолитной
футеровки ковша 15 плавок;
- техническая характеристика
ковша: высота – 4890 мм, ширина по цапфам – 4890 мм, ширина по носку – 5945 мм.
Согласно
вышеприведенным формулам имеем:
n = = 35,87 ковшей;
Nск = *(6,5+ )+1+1 = 16,1 ковшей.
Принимаю
в цехе 17 сталеразливочных ковшей.
1.2. Шлаковые чаши
Выбор емкости
чаш определяется количеством (объемом) образующегося на плавке шлака. Объем
шлака (Vшл)
на плавку можно рассчитать по формуле:
Vшл
= ,
где G - максимальная масса плавки, т;
Р - максимально
возможное количество образующегося шлака, % от массы плавки;
rшл
плотность шлака, т/м3 (изменяется в пределах 2,3…2,5 т/м3).
Количество
шлаковых чаш (Nшл)
определяется по формуле:
Nшч
= *1,15,
где ån - потребное суточное
количество шлаковых чаш без учета их оборачиваемости, шт;
1,15
коэффициент запаса;
tоб
время оборачиваемости шлаковых чаш, ч.
В настоящее
время при организации вывоза шлака с помощью шлакового пролета или крановой
эстакады время оборачиваемости чаш составляет 3…6 ч.
Максимальное
число шлаковых чаш без учета их оборачиваемости рассчитывается по формуле:
ånшч = * nшч,
где nшч – число шлаковых чаш,
шт.
Известно:
- максимальная масса плавки
250 т;
- на плавке образуется 15 %
шлака от массы плавки;
- шлак вывозится из цеха
через шлаковый пролет составами.
Тогда
на плавке образуется шлака:
Vшл = = 15,6 м3.
Принимаю к
установке на плавку под конвертер одну чашу емкостью 16 м3.
Согласно
приведенным выше формулам имеем:
ånшч = *1 = 35,87 чаш;
Nшч = *1,15 = 7,7 чаш.
Принимаю
для обслуживания цеха 8 чаш.
2
Крановое
оборудование
2.1
Разливочные
краны
Выбор
разливочного крана производится в зависимости от вместимости выбранного
сталеразливочного ковша, ширины принятого пролета и необходимой высоты подъема.
В общем
случае, суточная потребность в разливочном кране (åtРкр) определяется по
формуле:
åtРкр = ,
где N - число постоянно
работающих конвертеров;
tр – затраты времени на
собственно разливку одного ковша стали, мин;
tпр – затраты времени на
прочие операции, связанные с разливкой одного ковша, мин;
t - длительность конвертерной плавки, мин.
Затраты на
собственно разливку определяется прямым хронометражом или расчетом, или
принимается на основе справочного материала и рекомендаций проектных организаций.
При разливке стали со стенда затраты времени на собственно разливку не
учитываются (tр
= 0).
Затраты
времени на прочие операции зависят от: вида операций, выполняемых краном и
связанных непосредственно с разливкой стали; схемы грузопотока и конструктивных
решений отделения разливки.
Длительность
конвертерной плавки определяется из условия средней интенсивности продувки
металла (в проектируемом цехе равной 4,2 м3/(т*мин)).
Тогда:
Периоды |
Длительность,
мин |
Завалка
скрапа |
2,0 |
Заливка
чугуна |
2,0 |
Продувка |
17,14* |
Отбор
проб, замер температуры и ожидание анализа |
4.0 |
Додувка |
2.0 |
Слив
металла |
5.0 |
Слив
шлака |
2.0 |
Подготовка
конвертера |
3.0 |
Неучтенные
задержки |
3.0 |
ИТОГО |
40.14 |
·
-
определено расчетом:
t
= = 17,14
мин,
где
16,0 – длительность продувки при интенсивности 4,5 м3/(т*мин) [**].
Потребное
количество кранового оборудования определяется по формуле:
Nкр = ,
где
åtкр – суммарная суточная потребность в кране;
m
коэффициент, учитывающий затраты времени на вспомогательные операции.
Принимается обычно во всех случаях равным 1,15 (15% от времени основных работ);
С
коэффициент использования рабочего времени крана. Принимается равным 0,8;
24
число часов в сутках.
Известно:
ОНРС с линейным расположением машин, ширина разливочного пролета 16 м.
Принимаю:
- вместимость
сталеразливочного ковша 220 т [*];
- мостовой разливочный кран
с параметрами: грузоподъемность 280+100/20 т, пролет 15,5 м, высота подъема
крюков 36+36/40 м, скорость подъема 9,6+7,5/15,0 м/мин, скорость передвижения
главной тележки 30, вспомогательной 30 и моста крана 60 м/мин [*];
- разливка на машинах с
применением консольно-поворотных стендов.
Затраты
времени на прочие операции, связанные с разливкой одного ковша, для
рассматриваемого случая составят:
tпр = 7,38+7,38+20 = 34,76
мин,
где 7,38
затраты времени на перестановку ковша со сталевоза на разливочный стенд и
пустого – обратно, мин [*];
20 – средние
затраты времени, связанные с обработкой стали в отделении ковшевой обработки,
мин [*].
Согласно прведенным выше
формулам имеем:
åtРкр = = 20,78 ч;
Nкр = = 1,24 крана.
Учитывая
высокую загруженность и назначение, принимаю к установке в разливочном пролете
ОНРС с линейным расположением машин четыре разливочных крана.
Список использованных
источников
1.
Технология
производства стали в современных конвертерных цехах/ С.В. Колпаков, Р.В.
Старов, В.В. Смоктий и др. М.: Машиностроение, 1991.
2.
Металлургия
стали/В.И. Явойский, Ю.В. Кряковский, В.П. Нечкин и др. М.: Металлургия, 1983.
3.
Кудрин
В.А. Металлургия стали. 2-е изд. перераб. и доп. М.: Металлургия, 1989.
4.
Глинков
Г.М., Маковский В.А. АСУ технологическими процессами в агломерационных и
сталеплавильных цехах. М.: Металлургия, 1981.
5.
Заявка
и исходные данные на установку порционного вакуумирования стали -
Магнитогорский Гипромез, 1983.
6.
Технический
проект конвертерного цеха №1 ММК. Корректировка. Том 3 – Магнитогорский
Гипромез, 1988.
7.
ММК.
Основные направления развития металлургического комплекса до 2003 года
Магнитогорский Гипромез, 1995.
8.
Зиньковский М.М. Техника безопасности и производственная санитария. Краткий
справочник металлурга. 3-е изд. перераб. и доп. М.: Металлургия, 1984.
9. ММК.
Технологические решения по основному производству. Охрана труда -
Магнитогорский Гипромез, 1986.
10.
Злобинский Б.М. Охрана труда в металлургии. 2-е изд. М.: Металлургия, 1975.
11. Бринза
В.Н., Зиньковский М.М. Охрана труда в черной металлургии. М.: Металлургия,
1982.
12. Правила
безопасности в сталеплавильном производстве. 2-е изд. перераб. и доп./Под ред.
П.И. Гетьмана, И.Д. Чиграя и др. М.: Металлургия, 1984.
13. Ефанов
П.Д., Берг И.А. Охрана труда и техника безопасности в сталеплавильном
производстве. М.: Металлургия, 1976.
14. Внепечное
вакуумирование жидкой стали на комбинированной установке. Технологическая
инструкция ТИ101-СТ-ККЦ-71-2000. Магнитогорск: ММК, 2000.
15.
Поволоцкий Д.Я., Кудрин В.А., Вишкарев А.Ф. Внепечная обработка стали. М.:
МИСИС, 1995.
16. СНиП
23-05-95 Естественное и искусственное освещение. М.: Стройиздат, 1995.
17. ММК.
Реконструкция мартеновского цеха. Обоснование инвестиций. Пояснительная
записка. Том 4 – Магнитогорский Гипромез, 2001.
18.
Техническое задание на проектирование и изготовление МНЛЗ сечением 310 х 440 мм
Челябинский Гипромез, 1975.
19. Летимин
В.Н. Проектирование сталеплавильных цехов. Основные принципы, технические
решения и методика конструирования конвертерных цехов: Метод. указ. к самостоятельной
работе и дипломному проектированию. Магнитогорск: МГМИ, 1989.
20. Ахметшин
Н.Ф., Зинуров И.Ю., Галян В.С., Шумаков А.М., Киселев А.Д. Выбор параметров
трансформатора для агрегата «ковш-печь» и режимы обработки стали//
Электрометаллургия. 2001. № 10. С.23-26.
21. Якушев
А.М. Справочник конвертерщика. Челябинск: Металлургия, Челябинское отделение,
1990.
22.
Тахаутдинов Р.С. Производство стали в кислородно-конвертерном цехе
Магнитогорского металлургического комбината. Магнитогорск: 2001.
23. Летимин
В.Н. Выбор и расчет количества основного технологического оборудования
конвертерных цехов: Метод. указ. к практическим занятиям и дипломному
проетированию для студентов специальности 0401 специализации «Металлургия
стали». Магнитогорск: МГМИ, 1985.
24. Обработка
стали на установке «печь-ковш». Временная технологическая инструкция ВТИ
101-СТ-ККЦ-83-2000. ММК, 2000.
25. Внепечное
вакуумирование жидкой стали на комбинированной установке. Технологическая
инструкция ТИ101-СТ-ККЦ-71-2000. ММК, 2000.
(???) 26.
гипромезовская книга по АПК на немецком языке (переводная)…
27. Внепечное
вакуумирование стали./А.Н. Морозов, М.М. Стрекаловский, Г.И. Чернов и др. М.:
Металлургия, 1975.
28.
Конструкции и проектирование агрегатов сталеплавильного производства/В.П.
Григорьев, Ю.М. Нечкин, А.В. Егоров и др. М.: МИСИС, 1995.
29. Немцев
В.Н., Купфер Г.В., Савинова Т.Л. Оплата труда на предприятии: Метод. указ. для
самостоятельной работы по дисциплине «Организация и управление на предприятиях»
для студентов технических специальностей заочного факультета. Магнитогорск:
МГТУ, 2001.
30. Немцев
В.Н. Расчеты по оплате труда на предприятии: Метод. разраб. Для самостоятельной
работы по дисциплине «Организация и управление на предприятиях» для студентов
технических специальностей заочного факультета. Магнитогорск: МГТУ, 2001.
31. Немцев
В.Н. Расчет капиталовложений в инвестиционный проект: Метод. указ. для
самостоятельной работы по дисциплине «Организация и управление на предприятиях»
для студентов технических специальностей заочного факультета. Магнитогорск:
МГТУ, 2001.
32. Немцев
В.Н. Расчет показателей финансовой оценки инвестиционного проекта: Метод. указ.
для организации самостоятельной работы по дисциплине «Организация и управление
на предприятиях» для студентов технических специальностей. Магнитогорск: МГТУ,
2000.
33. Немцев В.Н., Летимин
В.Н., Сиволапов В.Г. Расчет производственной программы кислородно-конвертерного
цеха: Метод. указ. для студентов специальности 1101. Магнитогорск: МГТУ, 2000.
|